A németországi Alsó-Szászországban működő MAN Truck & Bus SE alkatrészgyártó üzeméhez tartozó logisztikai központ területe 1,1 millió négyzetméter. A VW konszernhez tartozó vállalat különböző alkatrészeket gyárt itt MAN és Scania típusú teherautóihoz, illetve buszaihoz. Emellett Európa nagy részét innen látja el a vállalat alkatrészekkel. A tengelyek előkészítésének területén a MAN 2018 óta a Jungheinrich vezető nélküli, automata rendszerét, röviden AGV-jét használja. Az AGV teljesen automatizált anyagáramlást biztosít a nyersanyagraktár, a gyártó terület 12 feldolgozó pontja és a készáruraktár között.
Az időveszteség minimalizálása
– Azelőtt a gyártósorokat hagyományos, manuálisan működtetett targoncákkal szolgáltuk ki. Ha a kollégáknak utánpótlásra volt szükségük, el kellett hagyniuk a munkahelyüket, hogy megkeressék a megfelelő alkatrészeket és maguknak kellett odaszállítani azokat. Ez sok időt vett igénybe, a dolgozók pedig tulajdonképpen nem a feladatukat végezték, hanem a non-produktív szállítási feladatokat intézték – mondta Walter Schwarze, a MAN Truck & Bus SE csoportvezetője.
– Az időveszteséget minimálisra akartuk csökkenteni és ezzel párhuzamosan a folyamatok hatékonyságát javítani. Döntő volt számunkra, hogy a megoldás tökéletesen, költséges módosítások nélkül kommunikáljon az SAP rendszerünkkel. A kiválasztott megoldás pontosan ezt nyújtja számunkra.”
A teljes megoldás testre szabható
A Jungheinrich az MAN részére egy testre szabott, teljes körű megoldást nyújtott, ami a vezető nélküli szállítórendszer (AGV) mellett a Traffic Managert, valamennyi SPS vezérlést, szenzorokat, valamint az AGV-re szerelt RFID szkennert tartalmazta. Az SAP csatlakozáshoz szükséges külső csatlakozási pontot is a Jungheinrich szállította. A hamburgi nagyvállalat saját fejlesztésű interfésze különösen fontos szerephez jutott, ez garantálja a kommunikációt a targonca és a raktárirányítási rendszer (WMS) között. Ez a köztes eszköz fogadja a szoftver kommunikációs központjából a megbízásokat és lefordítja, majd továbbítja azokat a targonca vezérlésének.
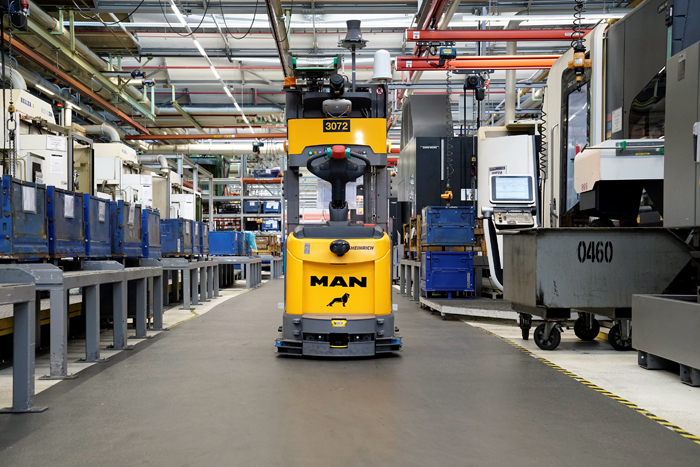
Az AGV közel 70 méteres szakaszt tesz meg a raktárak között.
Biztonságos és megbízható
A vezető nélküli targonca a reflektorpanelek segítségével automatikusan közlekedik a közel 70 méteres távon. Szkennerek és szenzorok garantálják a biztonságos üzemeltetést vegyes üzemben is. – Amennyiben a gép egy akadályt észlel, például egy másik targoncát vagy egy gyalogost, először automatikusan csökkenti a sebességét, majd pedig biztonságosan megáll. Amint az akadály megszűnik vagy eltávolításra kerül, az AGV automatikusan tovább halad. – „Számunkra az alkatrészek rendelkezésre állása a legfontosabb és a Jungheinrich automata megoldásának köszönhetően ez jelentősen javult” – nyilatkozta a cég szakembere. Az AGV nagyobb biztonságot jelent és jobban áttekinthető, tisztább munkafolyamatokat eredményez. – A számos előny és az eddigi pozitív tapasztalatok alapján biztosak vagyunk benne, hogy a jövőben az automata, vezető nélküli targoncák az üzemen belüli logisztika fontos alapját képezik majd vállalatunknál. Már most meghatároztuk a további alkalmazási területeket.”
A MAN Truck & Bus SE-nél 24 órás munkarendben dolgoznak. A folyamatos anyagáramlás biztosítása érdekében a Jungheinrich automata, vezető nélküli targoncája karbantartásmentes lítiumion akkumulátorral működik. Lehetőség van köztes töltésre is anélkül, hogy ez az akkumulátor élettartamát befolyásolná. – A töltés szintén teljesen automatikusan zajlik az AGV-n található kapcsolón keresztül. Amint az anyagáramlás lehetővé teszi vagy az akkumulátor töltöttsége indokolja, az AGV a speciális felszereltségű töltőállomásra megy, ahol néhány perc alatt gyorsan és biztonságosan feltölt – magyarázta Alexander Niek, a Jungheinrich projektvezetője. Az AGV így folyamatos rendelkezésre állást biztosít.
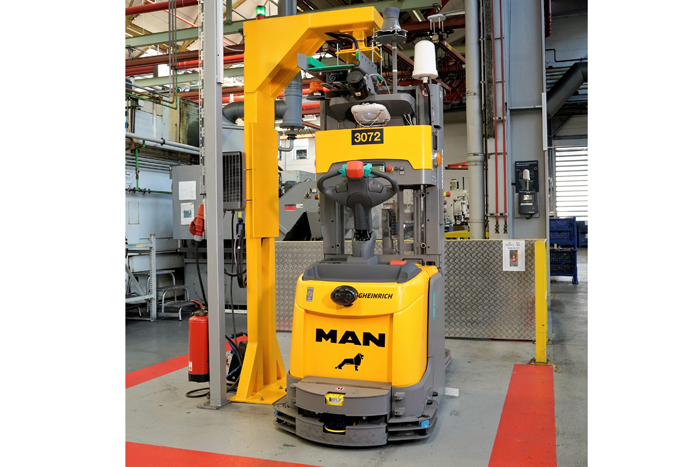
A Li-ion akkumulátor gyorsan, automatikusan feltölthető a töltőállomáson.
Teljes integráció „Güntherrel”, az új munkatárssal
Az AGV telepítése során a vállalat nagy hangsúlyt fektetett arra, hogy a dolgozók is elfogadják az új „munkatársat”, ezért a projekt elejétől fogva bevonták őket a folyamatba.
– Az automata robotrendszerek bevezetésénél mindig figyelembe kell venni az embert is. Egy ilyen megoldást nem lehet öncélúan bevezetni, hanem mindig meg kell mutatni az érintetteknek, hogy nekik milyen hasznuk van belőle. A dolgozók pozitív hozzáállása egy fontos sikertényező volt a projekt kivitelezése során – mondta Jonas Wullbrandt.
Ezért is döntött az MAN tudatosan a lépcsőzetes bevezetés mellett, melynek során a dolgozók szorosan együttműködtek a gyártó üzemben. Jelenleg az AGV-t már több mint egy éve, a hét minden napján három műszakban sikeresen alkalmazzák és teljesen elfogadták. – Munkatársaink hamar felismerték, milyen előnyöket biztosít nekik a rendszer a napi munkavégzés során. A kollégák nemcsak elfogadták a gépet, hanem meg is szerették és egy időközben nyugdíjba vonult kolléga nevére keresztelték – mosolygott a projektvezető Azóta „Günther”, a Jungheinrich ERC 215a automatája végzi a munkát az üzemben.