Nagy általánosságban a műanyag alkatrész könnyebb, és könnyebben, olcsóbban gyártható, mint a fém vetélytársa. Ezért plasztik rég a szívósor, és megannyi más alkotóelem, ami még 20-30 éve fémből készült.
Hiába a villanyautók előretörése, azért ez a folyamat nem áll le, a belső égésű motorokat is tovább terelgetik a hatékonyság felé vezető úton, és ennek jegyében most a szelepvezérlés környékén dobnák az alumíniumot.
A német Daimler és a MAHLE köré gyűlt fejlesztőcsapatok megoldása az integrált vezérműtengely modul, ami nem új találmány, a Volkswagen már évek óta alkalmazza például az EA288 kódjelű dízelmotorjainál. Lényege, hogy kevesebb alkatrésszel, alacsonyabb költséggel oldja meg a vezérműtengelyek rögzítését a hengerfejben, tulajdonképpen egy integrált keretről van szó, amiben minden adott a működéshez. Cserébe ha baj van, akkor kuka az egész egység, nem lehet az adott hibás bütyköt, csapágyat cserélni.
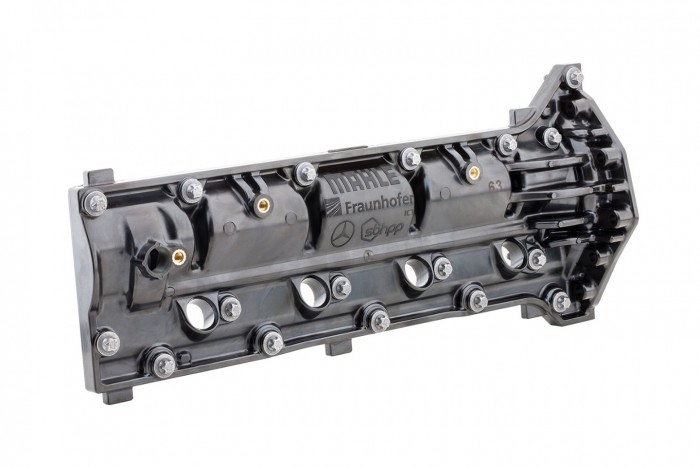
Állja a magas hőt, a rezgést, az igénybevételt, ráadásul könnyű, és olcsó. 600 órát bírt tesztmotoron, de vajon mi lesz a valóságban?
Ezt a gondolatot viszi tovább a hőre keményedő, szénszálas erősítésű műanyagból készült ház, ami annyi előnyt hoz, hogy csak kapkodjuk a fejünket:
- Könnyebb, ez egyértelmű előny, és mivel a motor tetején található, a tömegközéppont is lentebb kerülhet=sportosság?
- Jobban elnyeli a zajokat, mint az alumínium, ugye mindenkit idegesített már a benzinmotorok éktelenül csattogó vezérműtengelye?
- A gyártók kompletten kapják meg ezt az egységet a beszállítótól, és elég csak pár csavarral rögzíteni majd a motorra, gyorsabb lesz a gyártás.
- Előállítása kisebb szén-dioxid-lábnyommal jár, mintha alumíniumból készülne.
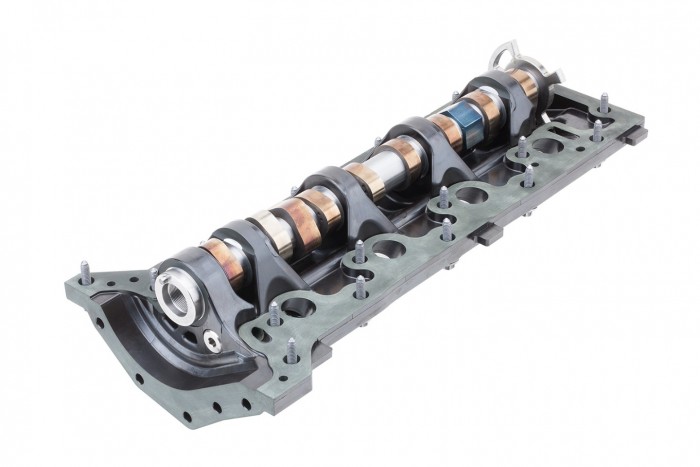
Ha itt valami balul sül el, mehet az egész a kukába. De miért lenne baj, ha úgyis lecseréljük az autót 150 ezer kilométer után?
Eddig hatszáz órát futtatták a próbadarabokat tesztmotorokon, és hiba nélkül vizsgáztak az új műanyagok, amelyek szilárdsága ugyan csak negyede az alumíniuménak, de ezt okos tervezéssel ellensúlyozták a mérnökök.