130 millió eurós beruházással új akkumulátorgyártó üzemrész kezdte meg a termelést a Škoda szülővárosában, Mlada Boleslavban. Ha egészen pontosan akarunk fogalmazni, akkor csupán összeszerelő üzemről van szó, hiszen maguk a cellák nem itt készülnek – ezeket az LG és CATL szállítja a gyárnak -, csupán a modulokat rendezik csoportba, egészítik ki vezérléssel, hűtőrendszerrel és csomagolják be masszív fémkalitkába, hogy aztán egy másik csarnokban bekerüljenek az elektromos Enyaq modellekbe.
Az itt készülő, különféle méretű és kapacitású akkumulátorok a Volkswagen-csoport elektromos járműveibe kerülnek – nemcsak a Škoda, hanem az Audi VW, SEAT is használ itt gyártott akkumulátorokat -, és ha rendesen beindul a gyártás, akkor 250 alkalmazott több mint negyedmillió akkumulátorcsomagot gyárthat itt évente. De ez még nem minden, a Škoda folyamatosan áll át elektromos autók gyártására – 2030-ig három új, méretben és árban is az Enyaq iV alatt maradó, teljesen elektromos modell várható a cseh márkától -, tehát nem áll meg a fejlesztés, a most elindított üzemet tovább bővítik, így 2023 végére már évi 380 ezer darab akkumulátorra nő a kapacitása. Emellett a németországi VW-üzem is egyre nagyobbra nő, ott 2023 végére tervezik a gyártás felpörgetését, hogy akár 600 ezer akkumulátor is elkészülhessen évente.
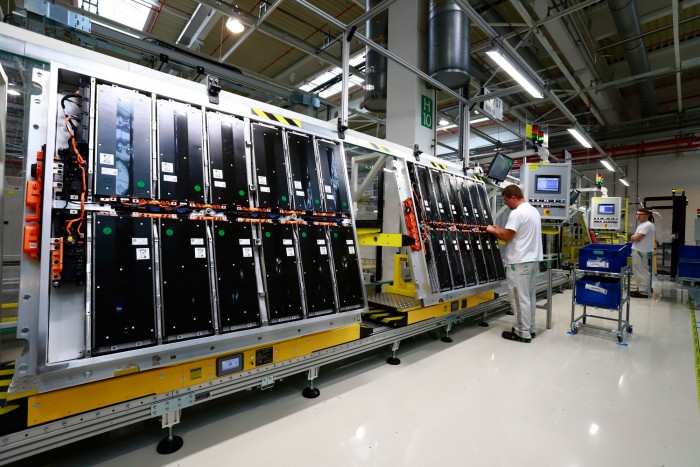
30 robot is segíti a 250 főnyi dolgozó munkáját
A Mlada Boleslav-i üzem Németországon kívül az egyetlen olyan gyártóhely Európában, ahol ilyen akkumulátorrendszereket gyártanak. Összesen háromféle lítiumion-akkumulátor található a portfólióban, a legkisebb, nyolcmodulos változat kapacitása 55 kWh, a kilencmodulos közepes méretű változat pedig 62 kWh-nyi energiát tárol. A legnagyobb, 12 modulból álló akkumulátor 82 kWh kapacitású. Az akksicsomagokon kívül az integrált hűtőrendszerrel ellátott akkumulátorház, az akkumulátorvezérlő rendszer és a szükséges elektromos csatlakozások is itt készülnek.
Nézegessetek gyártósort, így áll össze egy elektromosautó-akkumulátor:
Maga az akkumulátorgyártás közel sem annyira látványos folyamat, mint amihez egy autó- vagy éppen motorösszeszerelő üzemben hozzászoktunk. A gyárlátogatás hatalmas, üres, frissen műgyantázott placcon kezdődött. Meglepő, hogy ennyi szabad hely van egy üzemben, ahol általában a hatékonyságról, termelékenységről szól minden. Persze ez a terület sem fog sokáig kongani az ürességtől, a második fázisban többek között ezt a teret is be fogják lakni, hogy meglegyen az újabb 8000 négyzetméternyi gyártóterület a jelenlegi 18 000 mellé.
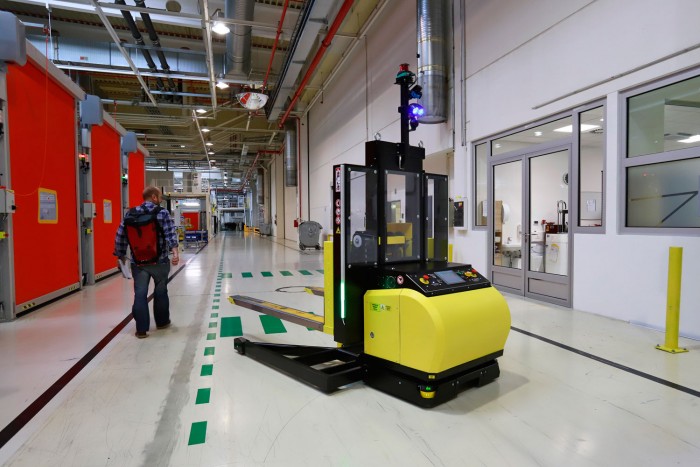
Önjáró targoncák hozzák viszik az alkatrészeket
Az első lépésként az akkumulátorcsomag fémváza érkezik meg, annak az aljára nyomnak a robotok hővezető pasztakígyót, ami nevéhez híven a használat közben keletkező hőt vezeti el a fémkeret aljában lévő csövekben keringő hűtőközeghez. A masszára ültetik az akkumulátormodulokat, majd következik az egységek összekötése és a vezérlés beszerelése. És persze rengeteg ellenőrzés, a 70 állomásos gyártósoron 16-nál folyik valamiféle ellenőrzés, vizsgálat. Jelenleg a soron 250 ember dolgozik három műszakban, őket 30 robot segíti ki azokon az állomásokon, ahol a robot munkája a jobb, gyorsabb, célravezetőbb.
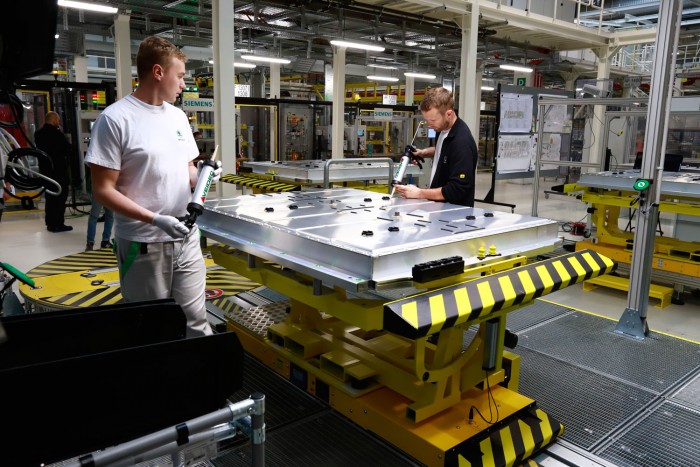
A két sziloplasztos ember zárja a munkafolyamatot
Ha minden rendben, akkor kékes trutyival tömítik a keretet, majd jön rá a masszív fémtető, amit rengeteg csavarral zárnak le, de az egység alja is kap mechanikai védelmet, ahol a hűtőfolyadék csatornái futnak. Innen újabb teszt következik, szigetelés, túlnyomásos és vákuumpróba, még egy kevésbé tudományos ízű sziloplasztos tömítés marad, amit két valódi ember végez, majd újabb utazás, már a raktár felé. Az állomások között önjáró szállítóeszközök végzik az akkumulátorok, alkatrészek mozgatását, de rafinált futószalagon is jönnek-mennek az alkatrészek, félkész termékek.
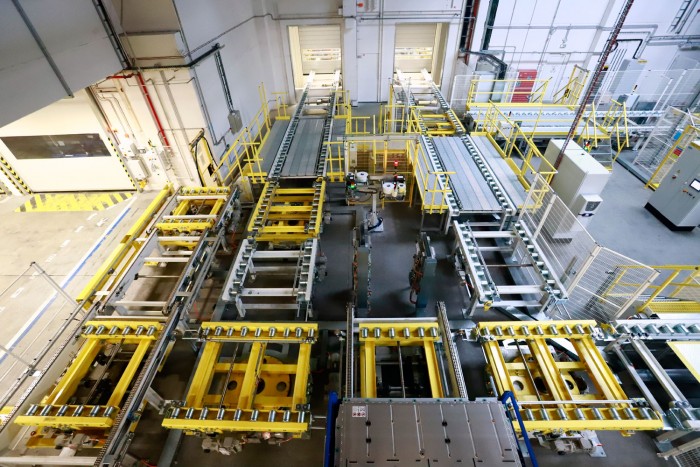
Bonyolult futószalag
Az akkumulátort gyártó sor után sokkal békésebb hely a raktár. Itt 3500 négyzetméteren halmoznak egymásra legfeljebb 3200 darab akkumulátort. Hogy ne okozhasson nagy galibát egy meghibásodott, túlmelegedő, ne adj’ isten kigyulladó egység, minden rekesznek saját hőkamerája van, ami figyeli a betárolt akkumulátorokat. A teljes raktározórendszer automatizált, de műszakonként azért 4-5 ember is felügyeli a folyamatokat. A veszély minimalizálása érdekében az itt tárolt akkumulátorok csupán 24 százalékosra töltve várják, hogy mintegy két kilométeres utat megtéve bekerüljenek a gyártósorra, ahol aztán egy Enyaq modell aljában kössenek ki.
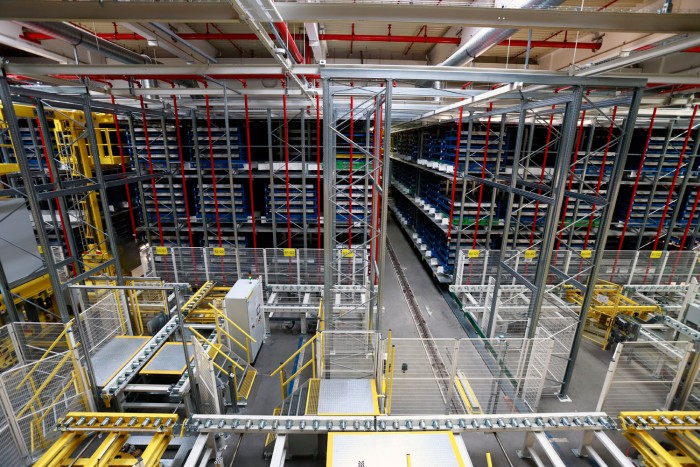
Hőkamerák figyelik a 24 százalékosra töltött, elraktározott akkumulátorok hangulatát
Ha érdekel, mi a teendő ha kigyullad egy elektromos autó akkumulátora, vagy hogy hogyan, milyen eszközökkel lehet ezeket eloltani, akkor itt mindent megtudhatsz:
Az 1995-ben átadott csarnokban a szerelősoron együtt, egymás után készülnek az Octavia és az Enyaq különböző változatai. Meglepő, ahogy ugyanarról a sorról gördülnek le ennyire különböző modellek, de az elképesztő munkatempó még érdekesebb. Sok autógyárat láttunk már, a zsúfolt, sötétebbtől a szürreálisan tágas és békés, komótosan ketyegőig. Itt az állomásokon lévő emberek száma megdöbbentő, szinte egymás lábára taposnak, még sincs összeakadás. De kell is a tempó, hiszen naponta úgy 1300 darab Škoda hagyja el a futószalagot. Jórészük ilyen olyan elektromos hajtással.