Az Audi idén is repülőre ültette és főhadiszállására, Ingolstadtba hívta a világ autós szaksajtóját, hogy megmutassa, mi is az a technológiai háttér, amitől olyan elképesztően tömörek, lehengerlőek, utánozhatatlan minőségérzetet árasztóak az autóik. Az idei Tech Day-en azt demonstrálták, milyen radikálisan alakul át az autógyártás a közeljövőben. Futószalag? Felejtős. Győrben hamarosan már kerekes robotok viszik a készülő autót szerelőállomásról szerelőállomásra.
A jelszó: Smart Factory
Manapság minden smart, a telefontól a mosógépen át az elektromos hálózatig, miért pont egy autógyár ne lenne az? No de mi lesz az Audi-féle Smart Factoryban az újdonság, amikor már ma is mindent behálózó informatikai rendszerek segítségével működtet just-in-sequence logisztikával valós idejű menedzselés mellett minden gyártó minden valamirevaló gyárat?
A legfontosabb változás, hogy a jövőben a német prémiummárka szakít a hagyományos szerelőszalagos autóépítéssel. A gyártástervező mérnökök úgy döntöttek: a számítástechnika van olyan fejlett, a vevői igények pedig vannak annyira különbözőek, hogy megérje egészen máshogy szervezni az összeszerelést. Ez lesz a
Modular Assembly,
a moduláris összeszerelés. Miközben a kivetítőn szemléltetve egy sematikus folyamatábrán néztük az új megközelítést, körülöttünk nagy zümmögéssel életre kelt a terem. Mert, mint kiderült, a kiállított A3, A4 és A5 karosszéria egy-egy teherszállító robot-alvázon feküdt, és ezek elkezdték a célállomásokra hordani az egyes épülő autókat szimuláló vázakat.
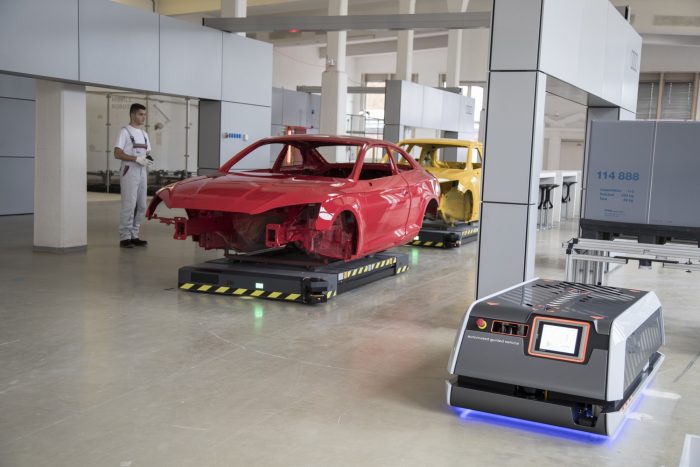
Robotok viszik a készülő autót, robotok hordják az alkatrészeker
Ugyanis a jövőben úgy lesz, hogy nem mozgó szalagon épülnek majd fel a kocsik, hanem szépen egyesével mozgatva, okosan megszervezve munkaállomásokon haladnak majd keresztül. Ennek egyik előnye, hogy minden egyes autó csak azokon a munkafázisokon megy keresztül, amikre valóban szükség van a specifikációjához. Vagyis ha egy-egy kocsit nem kell átvinni egy szerelési folyamat-elemen (például nem kerül bele tetőablak, követőradar vagy mondjuk AdBlue-tartály), eleve nem is megy oda, ahol ezt a szerelési fázist elvégeznék, ami logikusan felgyorsítja az összeszerelési folyamatot. Az Audi azt is kihangsúlyozta, hogy a szerelőmunkások számára is sokkal kevésbé stresszes egy rugalmas időbeosztású fix munkaállomás, mint a folyamatosan mozgó szalag.
A rendszer hátránya viszont, hogy nagyon-nagyon-nagyon precíz, folyamatosan alkalmazkodó, rugalmas tervezést igényel – de hát erre már megvannak a kellő kapacitású számítógépek és az öntanuló szervező szoftverek. A sok-sok autonóm anyagmozgatáshoz pedig megvannak a
Robotok és drónok,
amelyek mindig akkor és oda viszik majd az alkatrészt, vagy, mint láttuk, az épülő autót, amikor és ahova kell. Ennek szemléltetésére megismertük Paulát, az Audi saját fejlesztésű és gyártású robotját. Paula 1,2 tonnát tud mozgatni, egy speciális szállítókerettel ekkora tömeget tud „megfogni” és eltolni bárhová, ahová kell. Rádiós hálózat alapján navigál, de saját szenzorai is vannak, az akadályokat felismeri, kikerüli, képes jelzéseket értelmezni és kommunikálni a humán dolgozókkal a gyárban. Feltölti magát, ha lemerül, akár közvetlenül az emberektől, akár a gyártásszervező rendszerről fogad utasításokat, veszi az új feladatokat.
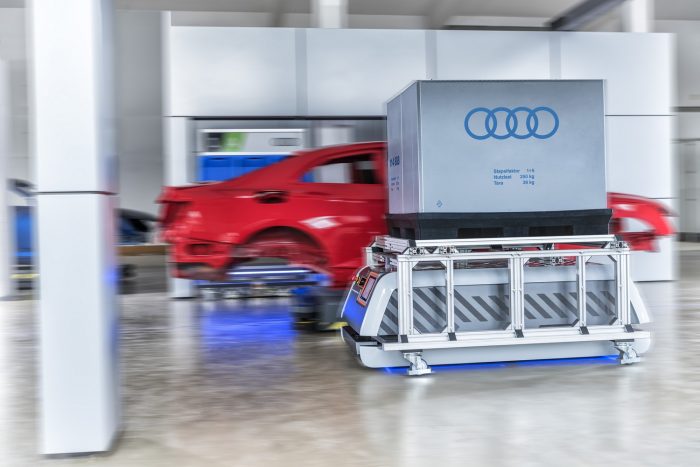
Paula szalad a ládával a szerelési ponthoz
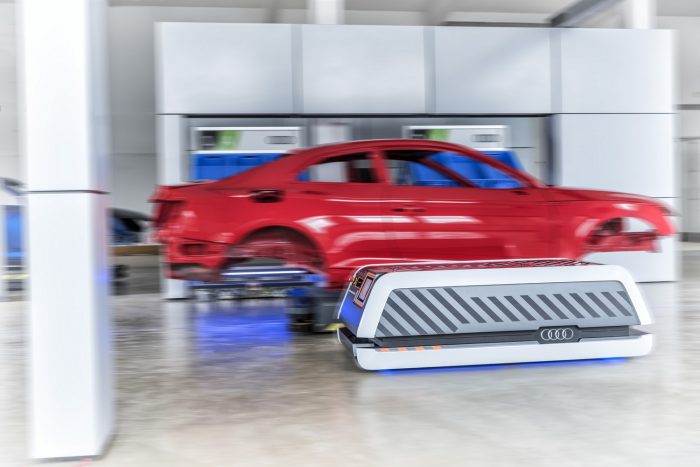
Paula, a robot: 1,2 tonnás, törvényileg limitált végsebessége 4,2 km/h
Nem tudom, Asimov boldog lenne-e vagy nyomna egy szomorú facepalmot, mindenesetre ezen a rendezvényen hallottunk a Robotika Első Törvényéről is, ami elég prózaira sikerült: Paula végsebessége ugyan 4,2 km/h. Lehetne ötször ennyi is, de nem lehet, mert az érvényes német szabályozás szerint robot nem haladhat gyorsabban ennél a kényelmes emberi sétatempónál. Érdekes.
Az Audi mutatott egy másik érdekes logisztikai rendszert is: ebben egy központi lézerszkenner és távirányított, két dimenzióban bármilyen irányban elmozdulni képes, centiméteres pontossággal navigáló minitargoncák vitték a ládákat egy adott munkaterületen. És persze ott vannak a drónok. Sajnos ilyet nem láttunk élesben, de a fotón nagyon jól néz ki, ahogy az Audi-kormányt egyenesen a beszerelő munkaállomáshoz repteti a propelleres robot:
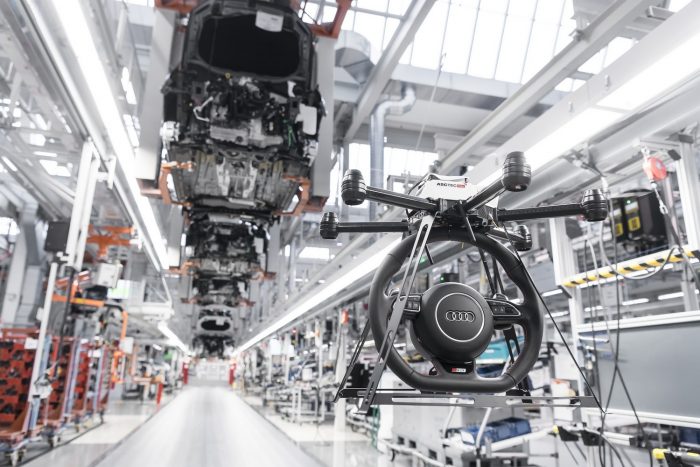
Drón viszi a kormányt a legrövidebb úton, a levegőben, toronyiránt a beszerelési pontra
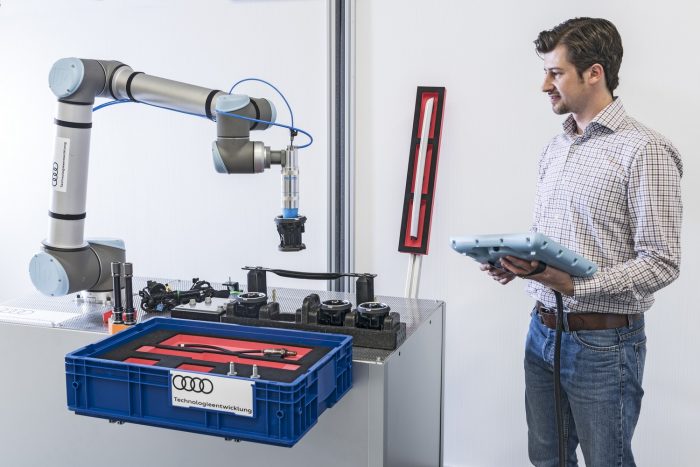
A Festo gumikúpos robotkarja precízen, érzéssel ragadja meg a változatos méretű, tömegű alkatrészeket
Láttunk egy olyan robotot is, amely azt szemléltette, hogy lesznek egyre ügyesebbek, univerzálisabbak az autóipari manipulátorok. A Festo készítette azt a gumikúpos, pneumatikus hogyhíjjákot, amely egy marék kis csavaranyát, egy darab Audi szellőzőrostélyt vagy egy négyes szettet kis tálcán, esetleg egy díszlécet, egy antennát vagy egy kábelköteget egyaránt meg tudott ragadni:
Na jó, a bowdent leejtette. Megnyugtató, hogy azért egyelőre még kell ember is az autógyártáshoz. Az ő munkájukat segíti az
Assisted Reality.
A Google Glass-os real-time munkafolyamat-vetítés vagy az esetleges hibák távgyógyítása (Győrben a technikus kamerás szemüveggel nézi a döglött robotot, Ingolstadtból a mérnöki konzílium elmondja, melyik panelt kell kicserélni) már nem is a jövő, ezeket a technikákat ma is használja az Audi. Viszont egyelőre még csak gondolkoznak azon, miként is lehetne legjobban hasznosítani a virtuálisvalóság-szemüvegek hálózatát.
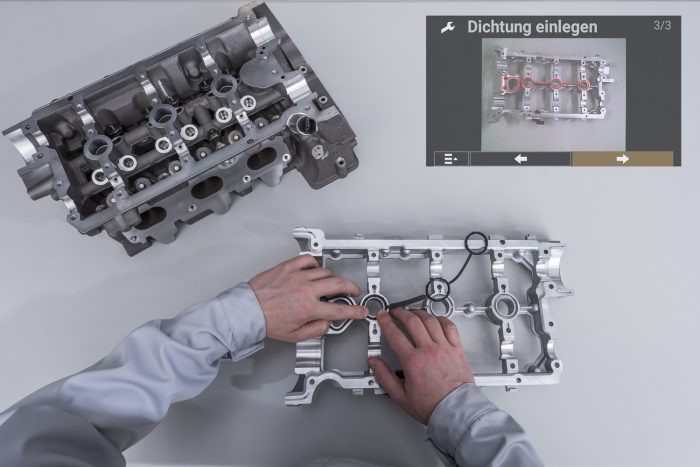
Google Glass-on követi a munkás a szerelési lépéseket
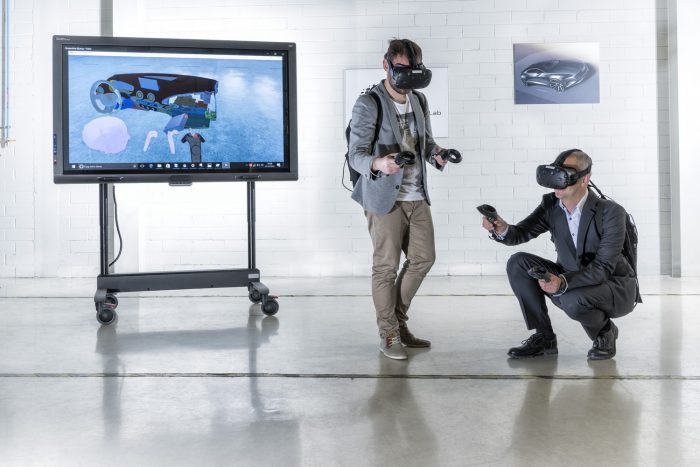
Virtuális térben összedolgozva tervezik a következő TT-t a dizájnerek
A bemutatón a vállalkozó kedvű kollégák (és akik nem hánynak azonnal, ha a szemüket teljesen befedő sisak alatt egy virtuális térbe zuhannak) nemcsak botladozhattak a 3D-grafikában egy készülő TT-makett körül, hanem felvehettek alkatrészeket, egymásnak adhatták őket a virtuális környezetben, 3D-ábrákat rajzolhattak virtuális filctollal a levegőbe és közösen ókumlálhatták ki, hogyan oldjanak meg egy szimulált tervezési hibát: a TT fejegysége túl hosszú volt, nem fért be a lemodellezett műszerfalba. A kétdimenziós képernyőn való tervezéshez képest sokkal átláthatóbb, valóságosabb a tervezőmunka, ha mindjárt körbe is lehet járni, a szemünk előtt forgatni és a többi alkatrész közé próbálni egy-egy új vagy átalakított munkadarabot.
A technológiai workshop legérthetetlenebb része a
Smart Analytics
modul volt. Nagyon sokszor elhangzott, hogy Big Data, sőt, Data Lake, az adatok óriási tava: irdatlan mennyiségű információ, amelyből emberek és szoftverek ügyesen kihalásszák az egyes gyártási folyamatok folytonos optimalizálásához a releváns összefüggéseket, következtetéseket. Sajnos ez a terület valami elképesztően unalmas, ha az ember nincs benne a témában évek óta és nem mélyült el az adattóban úgy, hogy csak az orra látszik ki belőle.
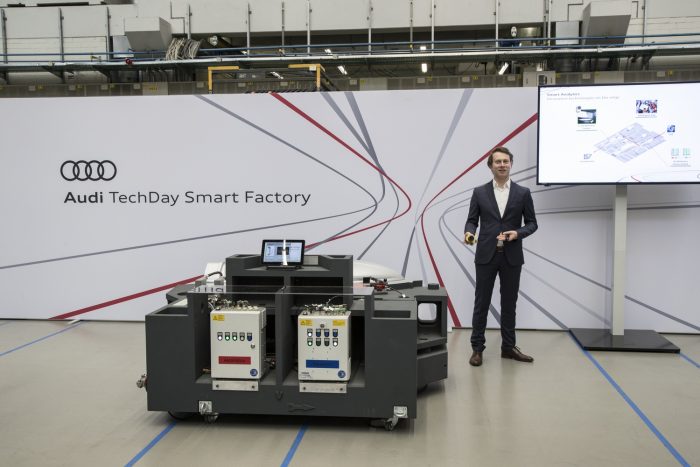
Ez a gép dolgokat mér. Sajnos nagyjából ennyit fogtunk fel a prezentációból
A monitoron vetített 40 000 soros Excel-táblától elerőtlenedve támolyogtunk át a témához kapcsolódó gépekhez, és grafikonokat kezdtünk nézegetni. Éreztem, hogy végképp az öntudatlanságba veszek, valamit tennem kellett. Minden bátorságomat összeszedve az előadó háta mögött egy hatalmas szerkezeten egy kis kart arrébb toltam, hogy végre történjen valami, hogy magam is becsobbanjak a Data Lake frissítő habjai közé. Ekkor egy lézerpötty arrébb ment egy kicsit, a kijelzőn pedig megváltoztak a számok és átmenetileg összeomlott egy EKG-szerű görbe, hogy aztán megint beálljon többé-kevésbé szabályos ritmusra. Na, ez már érdekes! Vajon mi történt? Egy anyagszerkezet-elemző nanorobotfalkának adtam új parancsot? Átprogramoztam az ingolstadti üzemet és mostantól Mercedes-emblémával jönnek ki az Audik a kapun? Esetleg kirúgtam kétezer munkást a mexikói gyárból?
De nem. Odahívtam az instruktort, megkérdeztem, hogy mit tettem, és ő megmondta: meglöktem – egy hőmérőt. Ami azt méri, 21,345235 vagy 21,345236 fokos-e az előtte álló pléhdarab, és a felfoghatatlanul apró változásokat jelzi ki folyamatosan a monitoron azon a cikcakkon. És akkor végre magunk mögött hagytuk a Big Datát és átmentünk a nap legérdekesebb helyszínére, megnéztük, milyen is a
3D-nyomtatás, fémből!
Az Audié a világ legnagyobb 3D metál-printere. A technológia egyelőre ott tart, hogy akár 44 cm (centiméter, igen) hosszúságú tárgyat is fel lehet építeni 50 mikrononként, rétegről rétegre. Lézer olvasztja hozzá védőgáz-fürdőben a por állagú titánt, alut vagy acélt a fájdalmasan lassan épülő alkatrészre. A folyamat időigényét elsősorban a céltárgy tömege határozza meg. Egy 3-4 kilós dolog úgy hat nap alatt készül el, de a technológiai fejlődést mutatja, hogy tavaly ilyenkor még 16 nap kellett hozzá az akkori legmodernebb gépben!
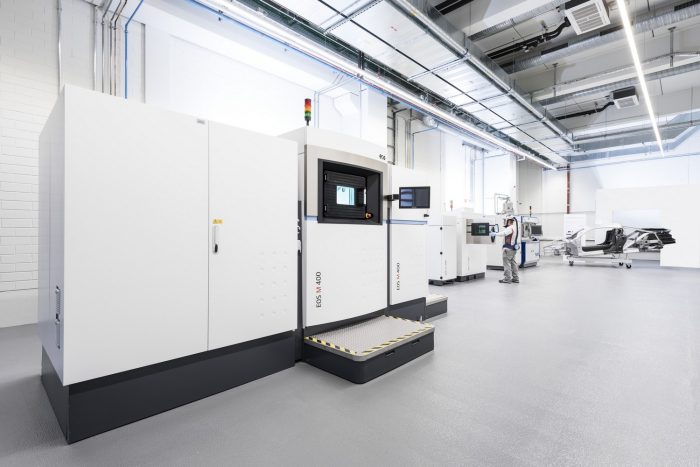
A közelebbi gép a világ legnagyobb 3D metál-nyomtatója, 44 centis dolgokat képes előállítani
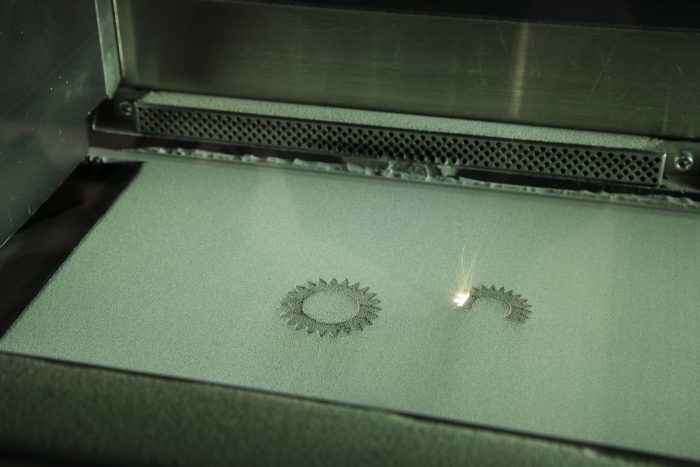
Rétegenként készül a fogaskerék a 3D-metálpinterben
A kémlelőablakokon át láttuk, ahogy kápráztató izzással alakul a lézerfény alatt a munkadarab. Mivel egy 3D-nyomtatott, fémből készült bármi ára jelenleg nagyjából százszorosa a forgácsolt vagy öntött alkatrésznek, egyelőre szerszámelemek készülnek az Audinál ezzel a technikával, de demonstrációs céllal egy R8-as vázának egyik teherviselő darabját is elkészítették nyomtatással. A hátsó kerék előtt, a legnagyobb terhelést kapó szerkezeteket összekötő teherviselő alumíniumelem tömege alig negyede a széria alkatrészének, de mechanikai tulajdonságai nem rosszabbak.

Ezeket a lezárt, kanyarított furatokat csak 3D-s technikával lehet belevarázsolni egy tömör alkatrészbe
Csak hát százszor annyiba kerül és nagyságrendekkel több idő elkészíteni – egyelőre. De nincs kétségem afelől, hogy pár év múlva az akkori Tech Day-en teljesen autonóm robotok már 3D-nyomtatott Audi-alkatrészeket hoznak-visznek a gyárban, lebegő szerszámok felszerelik őket a vázra, érzékeny gumiujjak elvégzik a minőség-ellenőrzést, majd a kész autó maga megy ki a címre a tulajdonoshoz, miközben hatalmas számítógépek már a következő A4-est vagy R8-ast tervezgetik mesterséges intelligenciájában a Big Data-tóból szerzett adatok alapján.
Persze jó kérdés, hogy mit fogunk akkor majd csinálni mi, emberek.