Ha a haszonjárműgyártók többsége kínál saját fejlesztésű váltókat, miért van akkor szükség olyan beszállítókra, mint az Allison? A válasz egyszerű: vannak olyan üzemeltetők, akik egyszerűen nem a gyárit, hanem az annál „jobbat” akarják. És a „jobb” szó itt és most szubjektíven kezelendő, hiszen nem tudhatjuk, hogy valóban jobb-e. Egy dologban biztosak lehetünk: az 1915-ben alapított amerikai cég jelenleg a világ vezető gyártójának számít a teljesen automatizált sebességváltók terén. Ugyan az európai tevékenységüket Hollandiából irányítják, az Allison mégis egyedül hazánkban rendelkezik gyártóbázissal kontinensünkön.
15 éve Magyarországon
A cég 2001 októberében nyitotta meg összeszerelő üzemét az ország nyugati csücskében fekvő Szentgotthárdon, akkor még az Opel Magyarország Kft. gyárában. 10 évvel később vadonatúj üzembe költözött át a város határain belül. A jelenlegi, 13 842 négyzetméter alapterületű gyárban a közepes teherbírású teherautókba szánt 3000-es széria, valamint a nehéz-teherbírású haszonjárművekbe építhető 4000-es széria váltói készülnek. De ugyancsak magyar kezek szerelik össze az autóbuszokba szánt Torqmatic automata váltókat is.
A Szentgotthárdon gyártott sebességváltókat széles körben alkalmazzák városi buszokban, az építőiparban, az áruszállításhoz használt járművekben, tűzoltó- és mentőautókban, terminálvontatókban, ingázó buszokban, hulladékgyűjtő, valamint egyéb katonai járművekben is. Hazánkban a Kravtex, a Molitus, valamint a MABI-Bus Kft. buszgyártó cégek építik be modelljeikbe az itthon készülő váltókat.
A gyárban jelenleg közel száz ember van alkalmazásban, ugyanakkor a munkások jó része az Opelhez tartozik, még a szükségszerű toborzást is a német konszern végzi. Globálisan nézve a cégnek az USA-ban, Hollandiában, Indiában, Kínában és Brazíliában van összeszerelő üzeme, melyek összesen 2700 embernek nyújtanak megélhetést. Innen nézve a magyar üzem talán kicsikének tűnhet, jelentőségét tekintve viszont egyáltalán nem az.
Mint egy autógyár
A szentgotthárdi gyár több részből tevődik össze. Az egyik legnagyobb területen – de mégiscsak egy csarnokban – az összeszerelő szalag helyezkedik el, mely felülnézetből nézve szabályos téglalapot tesz ki. Ez lényegében ugyanúgy működik, mint egy autógyáré: folyamatosan megy és egy-egy munkaállomáson a váltó csak néhány percet tölt el. A különbség annyi, hogy a munkafolyamat nincs annyira szétszabdalva, vagyis a munkaállomásokon nemcsak egy-egy alkatrész kerül a váltókba, hanem ennél jóval nagyobb ütemben haladnak.

Ez a gyártószalag eleje. Valahogy így néz ki a kezdetek kezdetén egy váltószerkezet.
A gép nem felejt
A szentgotthárdi gyár munkaállomásain előszerelés is folyik, azaz, amíg nem jön meg a következő sebességváltó, addig a dolgozónak elő kell szerelnie egyes beépülő elemeket. A munkaállomások szigorú ellenőrzés alatt vannak, így, ha egy alkalmazott akár egy csavarral is kevesebbet tesz a váltóba, akkor azonnal sípol a diagnosztika. A szerelőszalag legvégén megfelelő viszkozitású olaj kerül a váltóba, majd jön a próba, melynek során ki kell derülnie, ha valami nem működik jól.
A munka rutinszerű ellenőrzése érdekében ugyanakkor minden nap tetszőlegesen kiválasztva teljesen szétszerelnek egy váltószerkezetet, majd újra összerakják. Ennek leginkább a rutin szempontjából van jelentősége, hiszen szériahibára már nem nagyon derülhet fény, tekintve, hogy a 3000-es és a 4000-es sorozat is több mint 10 éve készül hazánkban. Májusban pedig a magyar üzem túl volt a 200 000. váltón.
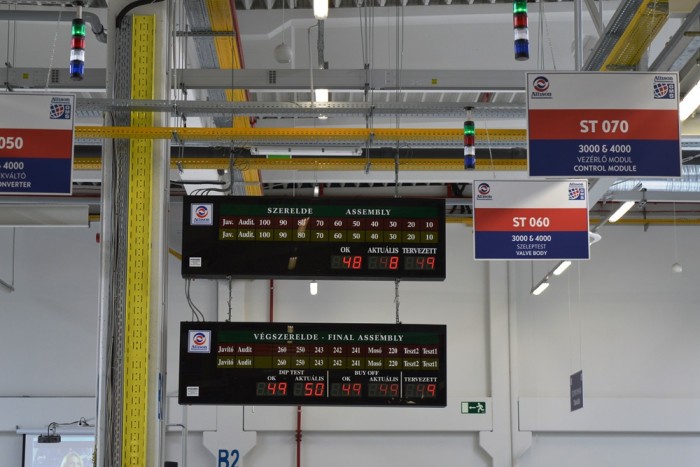
Az üzem éves kapacitására hiába kérdeztem rá, sajnos ezt hétpecsétes titkokként kezeli a cég, de annyi biztos, hogy folyamatosan, egy műszakban zajlik Szentgotthárdon a termelés.
Próba nélkül nem megy
A kipróbálás után a váltót speciális, vízzel teli kádba helyezik. A merülés után megfordítják, vagy visszaállítják eredeti helyzetébe. Ez a lépés azt a célt szolgálja, hogy fény derüljön egy esetleges hibára, hiszen, a váltóból kijutó oxigénbuborékok arról árulkodnának, hogy valahol rosszak az illesztések. Ha később mégiscsak felmerülne bármilyen gyártói felelősség, úgy a váltó gyártási száma segítséget jelenthet a probléma feltárásában, hiszen azt a cég a gyártást követő öt évig eltárolja. A vízpróbát követően a váltószerkezet megy a mosóba, majd végső kiszállításra várva a logisztikai részre kerül, ahol javarészt csupaszon, széles fémpolcokra helyezve várják meg a felkészítést az utazásra.
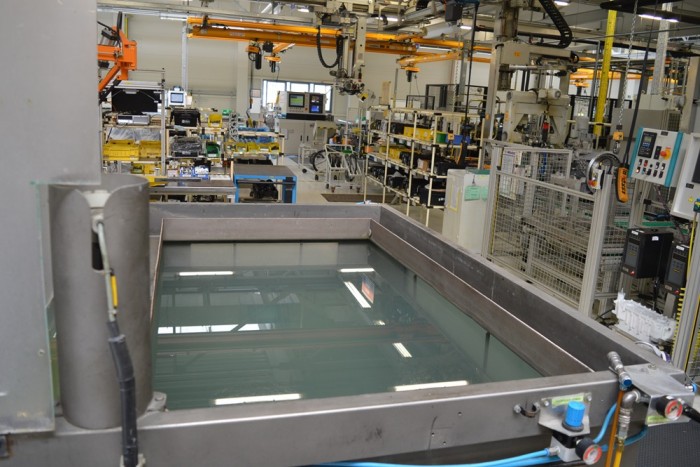
A gyártás során minden váltó egyszer víz alá merül.
Európa ránk figyel
És igen, itt jön a lényeg, melytől dagadhat a mellünk: az Allison a magyar gyárból szállítja több európai haszonjárműgyártóhoz a váltószerkezeteket. Oké, ez mégsem az IKEA, nyilván, az üzemeltetők nem építhetik be maguknak, de ahogy az elején is említettem, sok megrendelő nem a haszonjárműgyártók által kért váltót kéri, hanem az Allison valamelyik termékére bök rá. És nincs kivétel, az amerikai cég többek között a Daimler-csoportnak és a Scaniának is szállít, de számtalan olyan buszgyártó van, mely az Allison termékével kínálja modelljeit. Ottjártunkkor egyébként nem kevés Scania fadoboz állt a gyárban, ami annak is köszönhető, hogy a svéd gyártó éppen egy új modellgeneráció bevezetésének kellős közepén van.
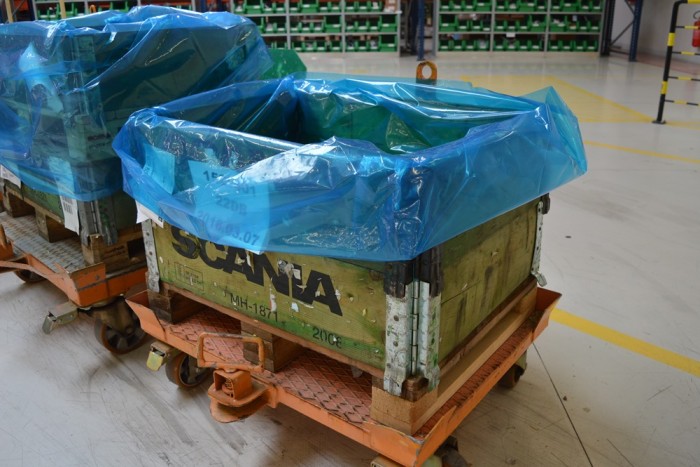
Már készülnek a Scaniának a csomagok Szentgotthárdon.
Saját tesztpálya
A cég komolyan gondolja közép-európai jelenlétét, amit mi sem jelez jobban, hogy 2012-ben megnyitották saját tesztpályájukat Szentgotthárdon. A létesítmény egyaránt szolgálja a rendszeres vásárlók, valamint a jövendőbeli ügyfelek igényeinek kielégítését. A pályán off-road, valamint országúti és városi terepviszonyokat szimuláló szakaszok váltják egymást. Külön hely van például a tolatás, a parkolás, valamint a gyorsulás kipróbálására is.
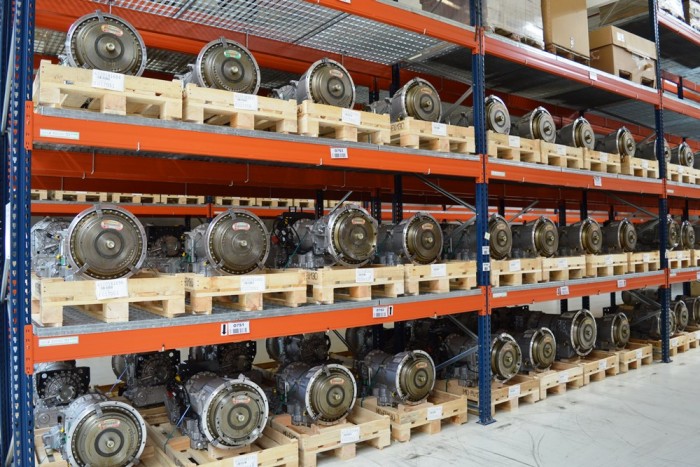
Az Allison még a brit Dennisnek is szállít Magyarországról.
Éles próba
Oké, most már azt is tudjuk, hogyan készülnek a váltók, de milyen teljesítményt nyújtanak a valóságban? A jó váltó definíciója könnyen meghatározható: a lehető leggyorsabban kapcsolja a megfelelő fokozatba a motort úgy, hogy közben a lehető legrövidebb ideig szünteti meg a motor és a váltó közötti kapcsolatot. Ilyenkor ugyanis az erőforrás üzemanyagot fogyaszt, nagyon nem mindegy tehát, hogy mennyi ideig tart egy váltás. A haszonjárművek váltószerkezeteinek ráadásul sok-sok tonnával kell megbirkózniuk, ezért kritikus szerep hárul rájuk az optimális nyomaték elérése érdekében.
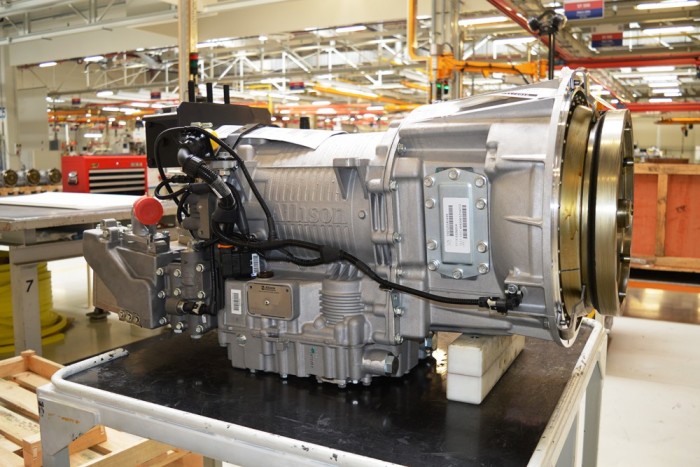
Így néz ki egy teljesen kész váltó.
A gyárlátogatás alkalmával többféle, teljesen automata Allison váltót lehetett kipróbálni különféle tesztjárművekkel. Lévén, hogy tízmillió buszszakértő országa vagyunk, két autóbuszra esett a választásom, melyek közül az egyik ráadásul idehaza készült.
Elsőként az ÉNYKK helyi viszonylatokon használt magyar gyártmányú autóbusza, a Credo BN12-es került sorra. A szóló buszban 263 lóerős Iveco erőforrás dolgozik, melyhez egy Allison 3000 GDP automata váltó csatlakozik. Ennek köszönhetően az elindulás protokollja a következő: először fékre tesszük a lábunkat, kiengedjük a rögzítőféket, majd D-be, azaz drive-ba kapcsoljuk a váltót, ezt követően felengedjük a féket és már adagolhatjuk is a gázt. Megdöbbentő érezni, mennyire könnyű városi autóbuszt vezetni a személyautóhoz képest még akkor is, ha az autóbusz teljesen üres volt a tesztelés alatt.
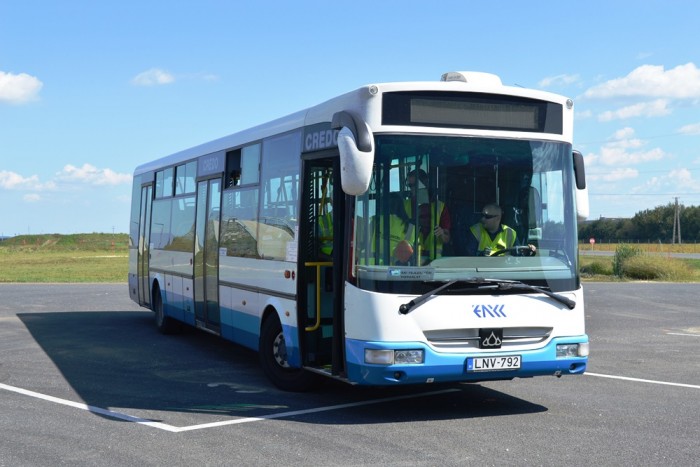
A kis Credo fürgén indult meg, ezért az első kört az ismerkedés jegyében inkább biztonságosan buszozva tettem meg a tesztpályán. A következő körben határozottabban adtam gázt, amire meglepő módon rendkívül dinamikusan válaszolt a hajtáslánc. Túlságosan nagy gyorsításokra azonban az ovális pályán nem volt lehetőség.
A következő egy turista kivitelű, török gyártmányú TEMSA MD9-es volt. Mivel a cég nem gyárt hajtásláncokat, kénytelen a versenytársak termékeihez nyúlni, ezért a Szlovéniából kölcsönzött buszban 250 lóerős, MAN D0836 típusú motor dolgozott, melyhez egy Allison T280R teljesen automatizált sebességváltó csatlakozott. A 9,3 méter hosszú buszt ugyanakkor még fürgébbnek éreztem a Credónál, ami főként annak köszönhető, hogy 2,5 tonnával könnyebb volt a hazai gyártású busznál.
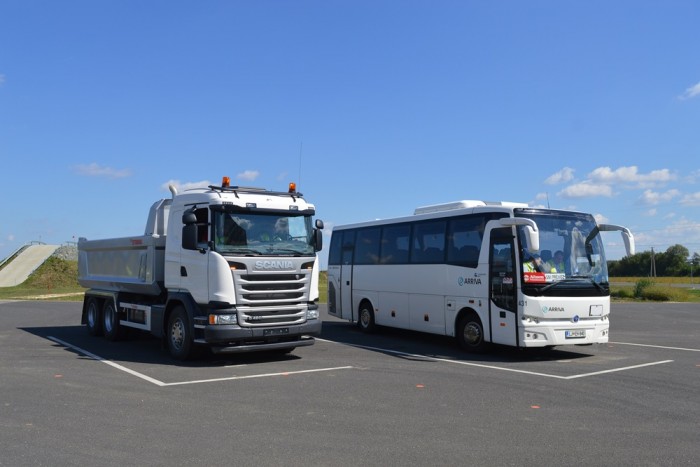
A jobb oldali TEMSA képes arra, hogy kedvet csináljon a buszsofőri hivatáshoz. Jól manőverezhető, technikája rendkívül alázatos, lényegében azt csinálja, amit a sofőr kér tőle a vezetőülésben. A nagy tükrökkel, valamint az Allison automata váltóval elképesztően könnyű tolatni vele.
Ugyan a hazai Allison-gyárban nincs külön fejlesztőrészleg, ettől függetlenül a szentgotthárdi gyár továbbra is lehetővé teszi a hazai ipar bekapcsolódását a világ haszonjárműgyártásába. A magyarországi buszgyártók pedig számolhatnak a kor igényeinek megfelelően megtervezett és összerakott váltókkal, melyekért nem kell annyit fizetni, mintha a tenger túloldaláról kellene őket ideszállíttatni. A cég szakemberei emellett készséggel állnak a hazai buszok fejlesztése során a megfelelő váltók kiválasztásárára, valamint azok optimális beillesztésére.