Szerteágazó az autóipar Magyarországon. Elég csak a három működő és egy épülő autógyárra gondolni, amik csak a jól látható elemei. Valójában az ország tele van kisebb-nagyobb autóipari beszállítókkal. Az ajkai kristálypoharaktól kezdve a Rolls-Royce belső kárpitelemeken át a Ferrarik karbonszálas burkolati elemein túl gombok, kapcsolók, csövek, elektronikai elemek, szinte minden készül nálunk. Gyártanak gumiabroncsot is, már öt éve Gyöngyöshalászon az Apollónál. Nemrég ellátogattunk az üzembe, ahol kiderült, az indiai vállalat magyar fejlesztőcsapatot állít fel.
Ördögi mágiának tűnik a gumiabroncs-fejlesztés külsős szemmel. A keverékek, rétegek, futófelületek, méretek zsonglőrjei között pedig a Gyöngyöshalászon első magyar fejlesztőként épp egy fiatal hölgy, Anita végzi ezt a feladatot a teherjármű-abroncsok területen. A férfiak uralta autóiparban nőként magasra jutni nem tűnik zökkenőmentes feladatnak. De amikor valakinek a hivatása a napi munkája, nem számítanak a nemek.
Anitával akkor találkoztam, amikor az öt éve működő Apollo gumigyárban körbevezetett minket. Nekem sokan mondták már, amikor beültem egy új autóba, vagy épp régibe, meséltem róla, vezettem, hogy csillog a szemem közben. Persze, ez az életem, a hobbim, a munkám, a szórakozásom. Amikor beléptünk a gyárba és megéreztem a frissen feldolgozott gumi szagát, nekem azért csípte a szemem, egy gumiabroncs-fejlesztőnek viszont ez a mámor, amit Anita nem is tagadott. Ezért úgy döntöttem, kifaggatom:
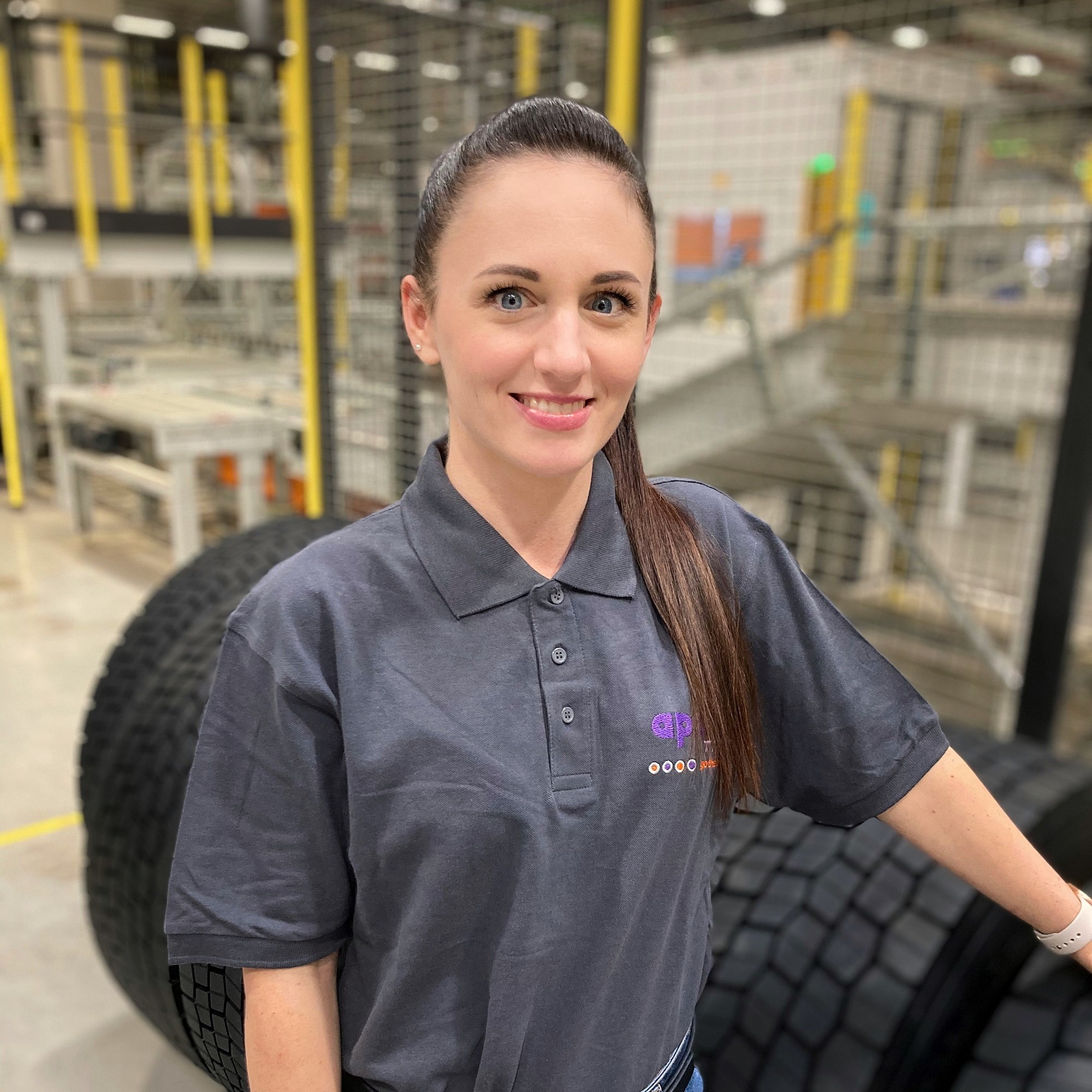
Anita öt éve dolgozik az Apollónál, mióta a magyar gyár működik, ő az első magyar gumiabroncs-fejlesztő a cégnél
Hogyan lett belőled fejlesztő egy gumigyárnál? – Vegyészmérnökként kezdtem a debreceni egyetemen, majd a műszaki egyetemen mesterdiplomáztam. Nem szakosodtam, de anyagtudományi szakirányon voltam mesterképzésen, és a tantárgyak között is volt gumiabroncsgyártás, amitől alapvetően is megtetszett ez az irány. Nem szerettem volna laborokban pipettákkal pár millis oldatokat csepegtetni egyik kémcsőből a másikba, ennél ez mindenképp egy izgalmasabb részleg.
Nagyon érdekes volt egyébként, ahogy idekerültem, mert a gyár akkor még nem működött. Egy konténerirodában volt az állásinterjúm, mert bár az épületek már álltak, teljesen üres volt még minden. Ez a zöldmezős beruházás már egyetemistaként is mozgatott, sok lehetőséget láttam benne, és látni egy gyárat működésbe lépni az első pillanattól kezdve, az nagyon izgalmasnak ígérkezett.
Mi a pozíciód, mióta dolgozol az Apollónál? – Öt éve vagyok a cégnél és egy karrierutat már bejártam. A technológiai csapathoz csatlakoztam kezdőként,gyakorlómérnökként. A kész gumiabroncsok tesztelési folyamatainak koordinálásáért voltam felelős, technológiai szempontból. Futási teljesítményteszteket, szerkezeti vizsgálatokat tartottunk, viselkedést vizsgáltunk és roncsolásos teszteket is végeztünk.
Másfél év után mentem át arra a területre, ahol összeépítik a termékeket, itt abroncsgyártó mérnökként dolgoztam. Ez után a kutatás és fejlesztési csapathoz kerültem át szintén abroncsgyártó mérnökként, de itt már egy lépéssel előrébbi állomáson dolgozunk a csapattal. Milyen legyen az abroncs, hogy nézzen ki, milyen széles legyen, meghatározzuk a paramétereit és a gyártási eszközökét is, például a sütőformáét.
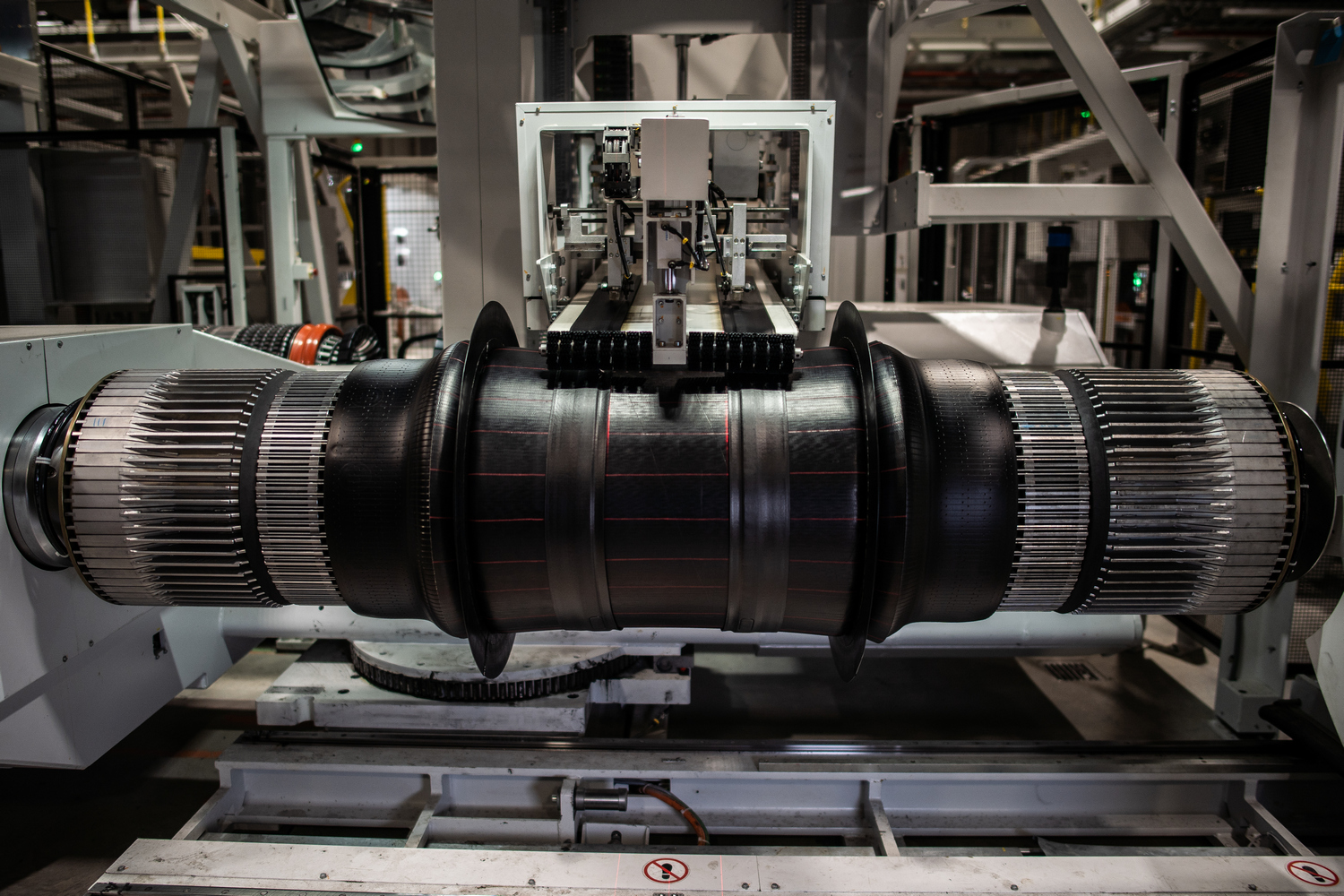
Az alkotóelemek összeillesztése automata illetve félautomata gépeken történik
Mivel foglalkozol pontosan, mivel telik egy napod? – Projekteket viszek. Három nagy része van ennek a munkának. Az egyik az alapanyagok, keverékek fejlesztése, a másik az új termékek bevezetése, a harmadik pedig a már meglévő termékek fejlesztése. Én az utóbbinál vagyok, ahol azokat vizsgálom, hogy a jelenlegi termékeink milyen teljesítménnyel futnak. Olyan szempontok között válogatok, hogy hol lehetne a terméket fejleszteni, például a súlycsökkentés, vagy a gördülési ellenállás csökkentése, a nedves és havas tapadás növelése, valamint az abroncsfutási teljesítmények növelése, hogy mennyit tud elmenni kilométerben.
Az Apollo-gyár
2017-ben épült az Apollo gyára zöldmezős beruházásként 470 millió euróból, és mára több mint 700 000 négyzetméteren folyik a termelés. A mondhatni vadonatúj gumiabroncsgyárban jártunk, ahol az Apollo és az itthon többek számára ismert Vredestein abroncsai készülnek. Előbbi leginkább az áruszállításban ismert, teherautókon, kamionokon, buszokon találkozhatunk vele, míg utóbbi név kerül a személyautó-abroncsokra.
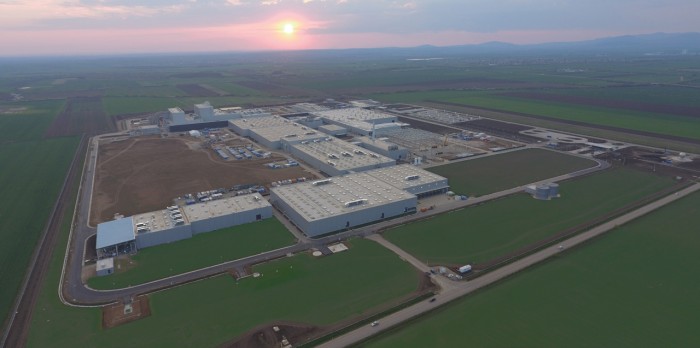
A gyöngyöshalászi gyárban valójában kettő különböző gyártósoron készülnek el a személy- illetve teherautó abroncsok
Az indiai tulajdonban lévő hazai üzemben 1100-an dolgoznak, 5%-ban külföldi, 95%-ban pedig magyar dolgozók, legalábbis egyelőre, ez az arány azonban folyamatosan változik. Évente 3 millió személyautó-abroncs és 7-800 ezer teherautó-abroncs készül el jelenleg. A többlépcsős folyamatban a keverék előállítása, a gumi feldolgozása, a rétegek összeillesztése, az abroncs összeépítése viszonylag gyors folyamatok, míg a vulkanizálás eltarthat akár egy óráig is egy teherautó-abroncs esetében.
Nem ez a legújabb gyár az Apollónál. 2017 óta Indiában is épült egy, így ott már öt üzemben készülnek a Vredestein és Apollo abroncsok. A gyártó európai központja pedig 2009 óta Hollandiában van a Vredestein korábbi üzemében, ami a magyar mellett szinte eltörpül 92 000 négyzetméteres területével. A fejlesztés nagy része Hollandiában, másik része pedig jelenleg Indiában történik, Gyöngyöshalászon pedig épp felfuttatják, nálunk lesz a harmadik nagy fejlesztőközpont, csak magyar fejlesztőkkel.
Hogyan működik a fejlesztés az Apollónál? Van külön magyar fejlesztőcsapat? – Két nagy kutatóközpont van, a teherabroncs-fejlesztés Indiában, a személyautó-abroncsok fejlesztése pedig Hollandiában folyik. A magyarországi központot egyelőre R&D Satellite-nak nevezzük, egy kis kutatócsapat, amit növelni fognak, és vélhetően mi leszünk hamarosan a harmadik fejlesztőközpont.
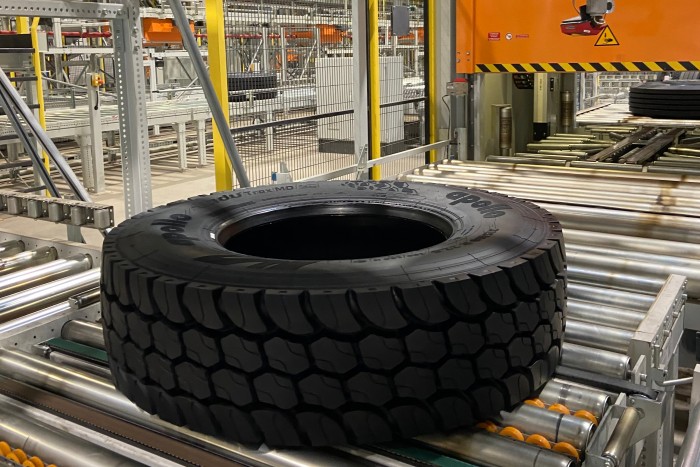
Egy nap alatt készül el egy abroncs, a haszonjárműgumiknál ez kicsit több idő
Milyen együtt dolgozni az indiaiakkal? – Nagyon kitartóak az indiai kollégák. Ezt már egész korán, az Apollóhoz kerülésemkor, a két hónapos indiai kiküldetésen tapasztalhattam meg, és ezt a fajta mentalitást hozták ide hozzánk is, adták át a magyar gyárnak. Addig mennek, amíg a probléma meg nem oldódik, nem adják fel, vagy lépnek át a dolgokon. Fiatal és lendületes csapat van nálunk, ahogy a gyár, úgy minden dolgozója is nagyon friss.
Mitől jó neked egy gumiabroncs? – Számomra a jó személyabroncs futás közben csendes és az adott felhasználási körülmények mellett biztosítja az elvárt biztonságérzetet. Teherabroncs esetében az elvárásaim között szerepel az alacsony gördülési ellenállás, mely következtében a teherautó fogyasztása és CO2-kibocsátása is csökken. A mai „zöld” irányzatok és későbbiekben a szabványok szigorítása következtében, ezen a területen kötelességünk jó, jobb és végül a legjobb teherabroncsot kifejleszteni.
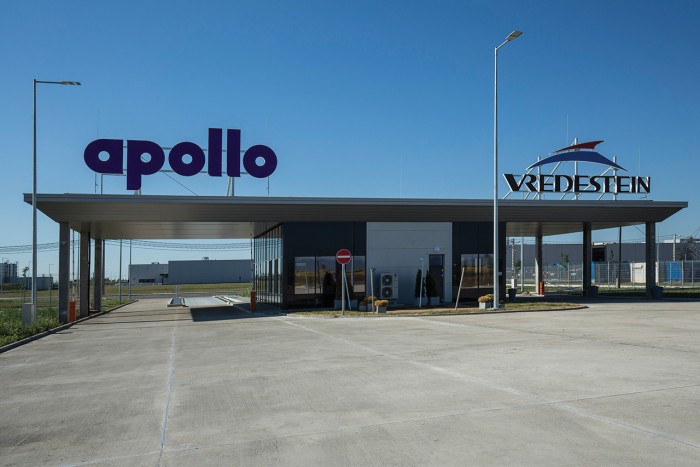
Az Apollo indiai tulajdonban lévő vállalat, amely 2009-ben vásárolta meg a holland Vredestein gyárat
Általában mekkora futás teljesítménnyel rendelkezik egy teherabroncs?– Míg egy hajtott keréken vagy pótkocsin használt abroncs 200 000 km fölött használódik el az első életciklusa végére, ez egy kormányzott tengelyen lévő abroncs esetében a funkciójából eredően alacsonyabb, 100 000 km fölötti érték. Az Apollo teherabroncsok élettartam tekintetében a versenyben lévő abroncsok között az élmezőnyben szerepel. Természetesen az abroncs funkcióján felül az abroncs életciklusát meghatározza a vezető által biztosított megfelelő használati körülmény, belső nyomás, valamint azon útvonalak minősége, ahol közlekedik.
Mennyi újrafutózást bír el egy teherautó-abroncs? Mi a leggyakoribb sérülés a teherautó-abroncsoknál? – Apollo teherabroncsok esetében a követelmény az első normál életciklusát követően még két újrafutózott használat, tehát az újrafutózásnak köszönhetően összesen háromszor olyan hosszan használhatjuk az abroncsot, mint az eredeti futófelülettel. A leggyakoribb sérüléseket tekintve első helyen állnak azon hibák, amelyek a futófelületet érintik. Egy-egy kisebb sérülés esetében a probléma fokozódhat, amennyiben a repedés mentén a víz eléri az erősítést végző belső acélszálakat, ezáltal elindítva a rozsdásodás folyamatát. Ennek következtében a maximális élettartam elérése előtt az abroncs meghibásodik. Ezen esetekben az újrafutózás lehetősége is veszélybe kerülhet, hiszen a régi futófelület lehorzsolását követően szigorú ellenőrzéseken megy át a teljes karkasz, melynél kizáró ok a rozsdás acélszerkezet.
Milyen nőként az autóiparban dolgozni? Nincs férfiuralom? – 21%-ban nők és 79%-ban dolgoznak férfiak az Apollónál. Nyitottnak kell lenni, ami főleg a kulturális különbségeket illeti, de én mindenféleképpen csak pozitívan csalódtam eddig. Abszolút nem érzem a nembeli különbségeket, teljesen egyenlő. A mérnöki szférában is teljesen összemosódik a férfi-női jelenlét, mint a divatnál, vagy egyéb területeken.
Rengeteg előnye van a női férfi vegyes csapatoknak. Sokan vagyunk nők, és én azt tapasztaltam, hogy ezt leginkább csak akkor vesszük észre, amikor megkérdezik tőlünk, hogy mi ezt hogy éljük meg. Nincs semmi tiszteletlenség, nem tesznek különbséget köztünk és a férfiak közt.
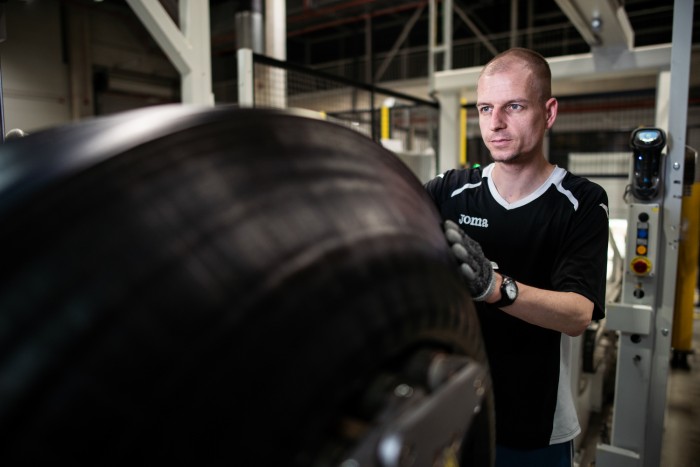
Vannak folyamatok, ahol ember által végzett ellenőrzés is van, mint például a félkésztermékek összeillesztésénél
Van most valami nehézség a gumiabroncsiparban, mint az autóknál a chiphiány? – Jelenleg ilyen nincs. Volt olyan a Covid-járvány elején, hogy egy hónapra leállt a gyár, de nem volt semmiféle megszorítás. A leállás is csak a járvány miatt történt. Utána volt egy alapanyaghiány, de amiatt nem állt le a gyártás, szereztünk máshonnan. Olyan például nem volt, aminek a hatására visszaesett volna a termelés, évről évre egyre magasabbak a számaink. Vannak olyan napok, ahol feltolják a termelést a maximumig, hogy megnézzék, mennyi lenne a legtöbb. Ha bármiféle probléma lenne az ellátással, akkor ilyen nem történhetne.
Így készül a gumi az Apollónál
Számtalan fő- és mellékfolyamat található, amelyek sokszor párhuzamosan futnak egymás mellett, amíg megkapjuk az általunk már olyan jól ismert gumiabroncsot. Mégis, ha össze kellene foglalni röviden a folyamatot, akkor az alapanyag-felhasználásnál kell kezdeni.
A zárt és nyitott keverőkben meghatározott körülmények mellett összekeveredik a polimer, a különböző kemikáliák és töltőanyagok (pl. korom), valamint a térhálósító ágens (vulkanizáló szer), melynek eredményeként megkapjuk a kilapolt gumiréteget. A kapott keverék két különböző fő területen kerülhet további felhasználásra: a kalanderen vagy az extrúderen.
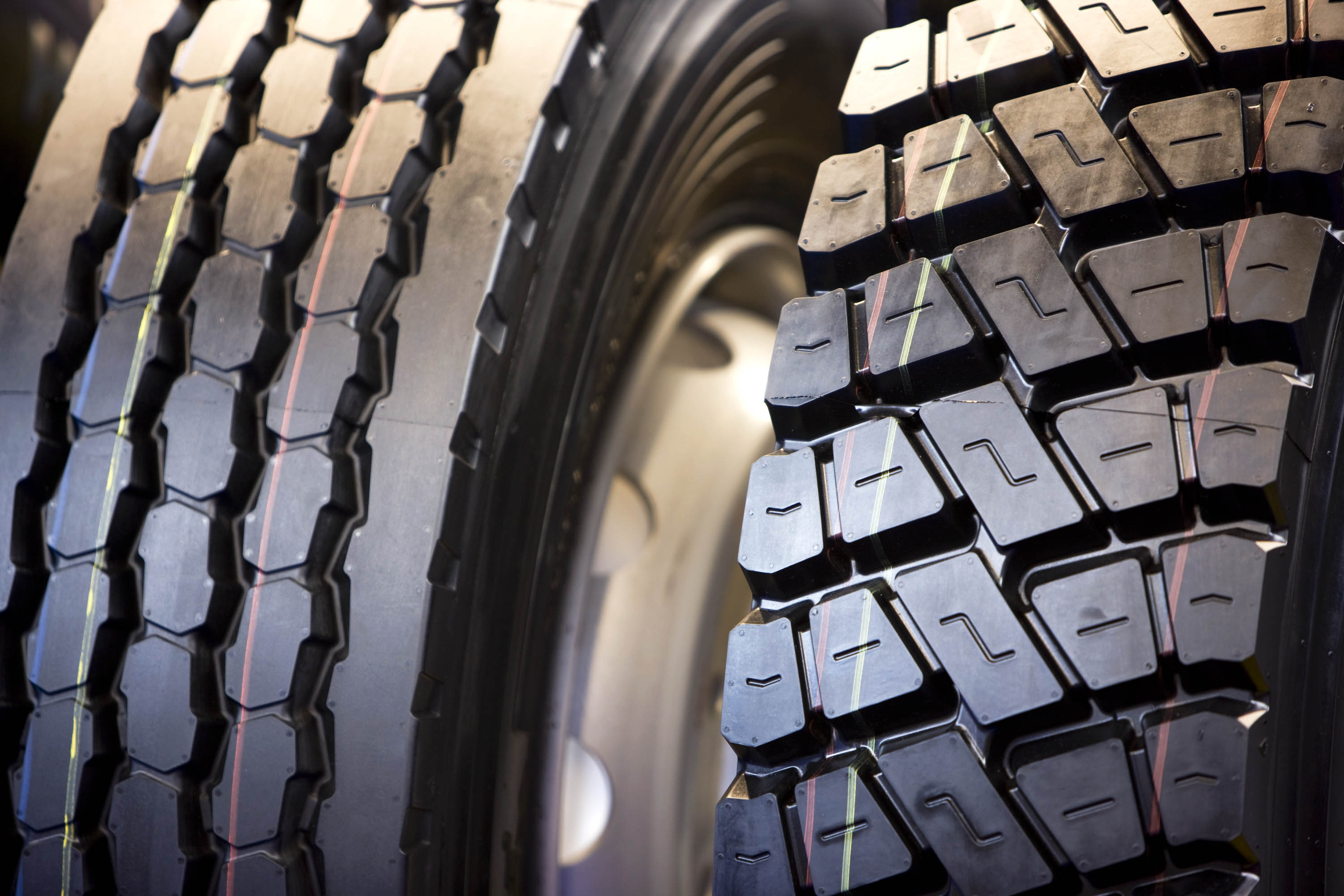
A személyautó-abroncsok kb 15 percet töltenek a vulkanizálóban, a teherautó-abroncsok viszont van, hogy egy órát
Míg a kalanderen két gumiréteg közé préselve készül el a textil- vagy acélszál-erősítéssel rendelkező termék, addig az extrúderen a gumikeverék különböző szerszámon préselődik át, melynek eredménye a profilozott félkésztermék. Mindeközben a peremkarika tekercselése is zajlik. Amint az összes félkésztermék elkészül, már el is kezdődhet az úgynevezett „zöld” abroncs* összeépítése. Az építés során a megadott specifikációknak megfelelően a félkésztermékek precíziós összeillesztése történik.
Ennél a folyamatnál a specifikáció betartásának kiemelkedő szerepe van, mivel akár 1 cm-es levegő, levegőbuborék is okozhatja a végső termék leselejtezését. Az egyes folyamatok közötti anyagszállítás többnyire automatikusan, robotok segítségével valósul meg, mint ahogy a „zöld” abroncs szállítása is a sütőformákhoz. Itt veszi kezdetét a vulkanizálás, mely folyamat során megtörténik a polimer térhálósodása, így a képlékeny, plasztikus tulajdonságú kaucsukból rugalmas, elasztikus vulkanizált gumi jön létre.
A gumiabroncs kisülése után már csak a végső minőség-ellenőrzési lépések vannak hátra: vizuális ellenőrzés, uniformitás és kiegyensúlyozottság-ellenőrzés, valamint teherabroncsok esetében röntgen átvilágítás. Az említett ellenőrzési pontokon minden egyes abroncs átesik, és megfelelő minősítést követően a termék forgalomba hozható.
Mit szeretsz a leginkább a munkádban? – Szívem szerint sok mindent kiemelnék, de amit a legjobban szeretek, az az, hogy minden nap új. Ugyanolyan rugalmas a mindennapom, mint maga a gumi. Az alapanyag rengeteget változik, ezzel a megoldandó feladatok is folyamatosan változnak. Sosem volt olyan napom, hogy azt éreztem volna, hogy unatkozom, vagy ezt már százszor csináltam. A cég is elég rugalmas, bármerre tovább lehet lépni, rengeteg a lehetőség. Emellett pedig elég dinamikus munkahely, pont olyan, amilyen én is vagyok.