Számos olyan, a konkrét gyártósoroktól távol álló tevékenység zajlik már az Audi győri gyárában, melyekről korábban azt gondolhattuk, hogy mindez ingolstadti íróasztalok mögött dől el, a magyar melós feladata pedig az, hogy előkészítse egy robot számára az összeszerelni kívánt elemeket. Az Audi felismerte, hogy érdemes a hazai szürkeállományra is nagyobb hangsúlyt fektetnie. Így jött létre az Audi Hungária Shared Competence Center (SCC) közel 800 munkatárssal. Nemrég megmutatták nekünk, mivel is foglalkoznak, sőt, ki is próbálhattuk magunkat egy-két téren játékos formában.
Az angol nevű központ kiemelt kompetenciát igénylő szolgáltatásokat kínál többek között a beszerzés, az informatika, a pénzügy, a logisztika, a kontrolling és a járműfejlesztés területén. Az így megszerzett tudást nemcsak itthon, hanem a teljes Volkswagen-konszernen belül felhasználhatják: jelenleg nyolc márkával állnak kapcsolatban (Audi, VW, SEAT, Porsche, Škoda, Lamborghini, Bentley, illetve a kínai FAW-konszern).
Kaptunk például 15 ezer eurót, hogy szereljünk fel néhány extrával egy Audi S1 Quattro LEGO-autót. Persze nem tetszés szerint: voltak kötelezően felszerelendő elemek, illetve minden alkatrésznek megvolt az ára. A cél természetesen a profit maximalizálása volt. Különféle csomagajánlatokban is gondolkodhattunk, de nem volt több egy tucatnál az összes választási lehetőség. Ennek ellenére meglepően nehéz volt megoldani a rögtönzött autóépítő feladatot.
Ezen tevékenység valós viszonyokra átültetett változata a kontrolling területéhez tartozik: ők adnak pénzügyi tanácsokat a részlegeknek, financiális célokat határoznak meg, anyagköltségeket számolnak – 2019 óta már az egész Audinak. Idén például 1 milliárd euróra rúg ez az összeg, ennyi pénzt költenek csak autóalapanyagokra.
Nem mindegy azonban, hogy mire költik azt a pénzt. Ez már a beszerzés feladata, ahol az elmúlt időszakban a koronavírus-járvány és az orosz-ukrán háború hatásai is megnehezítették a munkát. Győrből határozzák meg tehát, hogy honnan jöjjön a nagyjából 33 ezer különféle alkatrész éves szinten mintegy 2,5 milliárd euró értékben hat márka számára, melynek egy részét a magyar ipar szolgáltatja: körülbelül 150 magyar beszállítója van a VW-konszernnek, ebből 80 közvetlenül az Audi Hungáriának is szállít.
Külső szemlélőként ezek kevésbé izgalmas területek. A látványos dolgok a jármű- és járműhajtás-fejlesztési részlegeken találhatóak Itt már nem az irodai munkán van a hangsúly: terepen, azaz az üzemi épületekben, műhelyekben várnak a feladatok, valódi alkatrészekkel és autókkal. Van is bőven teendő, tekintettel arra, hogy a két részlegen összesen 550 ember dolgozik, méretüket tekintve pedig a harmadik legnagyobb műszaki fejlesztőrészlegét alkotják az Audi házán belül.
A járműhajtás-fejlesztés különböző benzin- és dízelmotorok, valamint elektromotoros tengelyhajtások teljes körű fejlesztési projektjeivel foglalkozik, a tervezéstől a fékpadi tesztelésig mindent ideértve. Mindehhez szükség van speciális infrastruktúrára: többek között 17 belső égésű motorok vizsgálatára használt fékpadra támaszkodhatnak. Ezen felül található még itt 3 villanymotoros tengelyhajtások vizsgálatára használt fékpad, 2 akusztikai és 1 klímafékpad is.
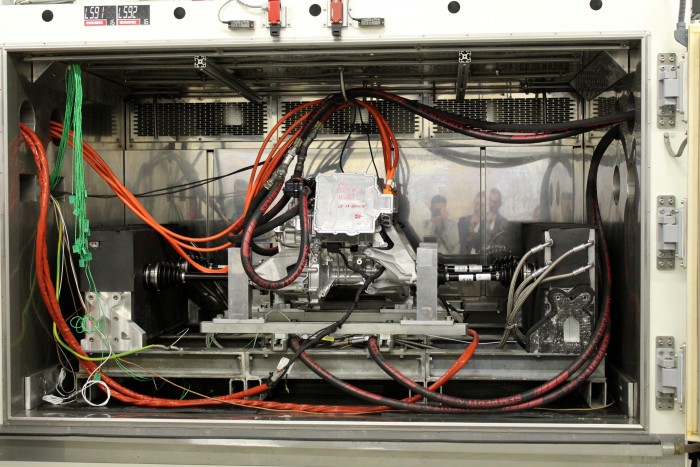
Az elektromos erőforrások összeköttetésben állnak egymással a fékpadon: miközben az egyik hajtás motor üzemben hajt, a másik generátor üzemben fékez
Meglepően nagy gépparknak tűnhet ez, de igénybe is veszik az eszközöket: az Audi többi gyárában csak azokat a motorokat tudják tesztelni, amelyeket ott készítenek, máshoz nincs meg az infrastruktúra. Győrben azonban megvan minden ahhoz, hogy bármilyen Audi-motort tesztelhessenek, amely napjainkban készül. 2021-ben egyébként 1,62 millió motor készült az Audi Hungáriánál.
Az imént említett eszközlétszám még nem végleges, ugyanis a következő évek során két számjegyű eurómilliós összeget fordítanak a fejlesztésekre. Ennek keretében a meglévő fékpadokat korszerűsítik, de érkezik egy teljesen új darab is az elektromos tengelyhajtások és a hozzájuk tartozó áttételek fejlesztéséhez.
A részleg látványosságai közül a villanymotorok járatópadját és az akusztikai járatópadot vehettük közelről szemügyre. A villanymotorok padján rögtön nem is egy, hanem két motor tesztelése zajlik egyidejűleg. Az erőforrások összeköttetésben állnak egymással, és miközben az egyik hajtás motor üzemben hajt, a másik generátor üzemben fékez. A rendszer így rendkívül energiahatékonyan tud működni. A két erőforrást 1000 üzemóra alatt 300 ezer kilométernyi gyűrődés, használat éri.
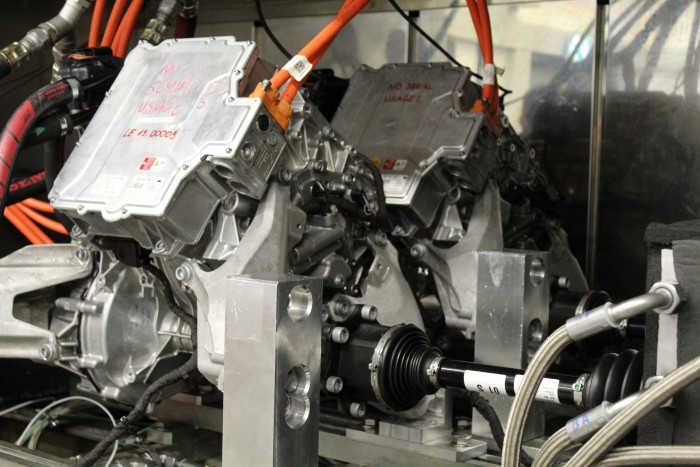
Hátul ott bújik a második hajtás is
Az akusztikai járatópad egy teljesen hangszigetelt szobában kap helyet, ahol szintén lehet akár egyszerre két villanyhajtást működtetni. A fékezőmotorok egy másik helyiségben kaptak helyet, ezzel is minimalizálva a terem zajszintjét. Egy akusztikus kamera végzi a munka dandárját: a furcsa szerkezet ernyőjén 60 érzékeny mikrofon található, melyek segítségével az észlelt hangokat vizuális formában is meg lehet jeleníteni. Egy program színes ábrákat vetít a hagyományos módon rögzített képre a hangok erősségének megfelelően. Többféle viselkedést képes szimulálni ez a rendszer, például a kanyarban fékezést is.
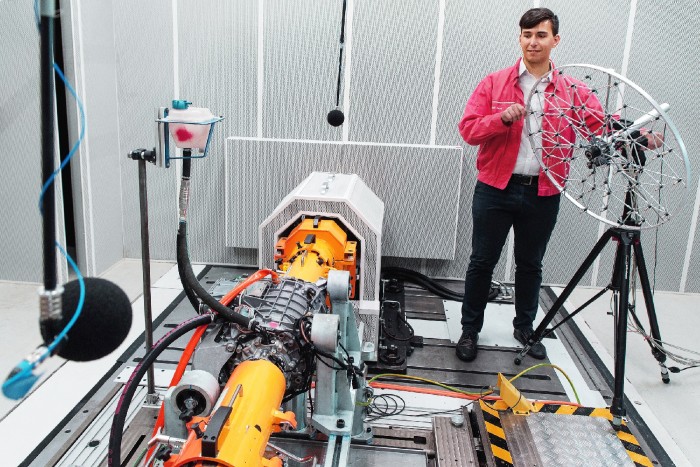
Jobb oldalon az akusztikus kamera, 60 mikrofonnal az ernyőjén
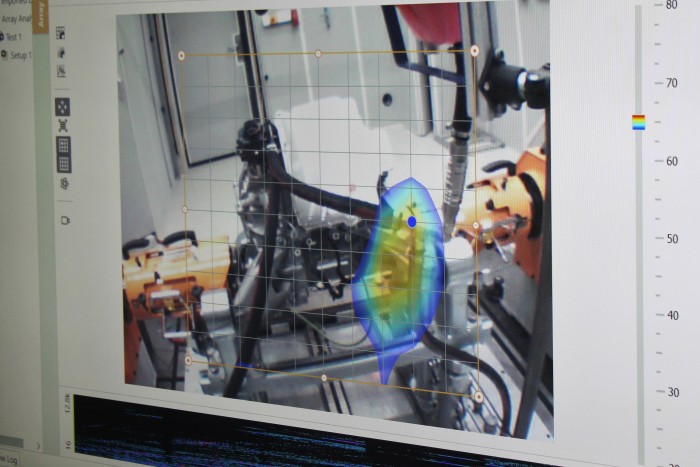
A képen látható színes paca az akusztikus kamera felvétele. Itt épp a megjelölt terület irányából jött a hang
A járműfejlesztésnél már az autókoncepciók kidolgozásának szakaszában elkezdik keresni a válaszokat a hő- és energiaelosztásra vonatkozó kérdésekre. Gyakorlatilag a felhasználói visszajelzések kvantifikálása zajlik, azaz az adatok és számok nyelvére próbálják lefordítani, milyen is a jó autó a vevő szerint. Ha ez megvan, akkor már „csak” abban kell bízni, hogy az akusztikai vizsgálóteremben és a fékpadokon is a várt számok jöjjenek ki eredményül.
Teljesen nem szakadhatunk el az erőforrásoktól ezen a részlegen sem: itt található a szerkezet, melyre cikkünk címében is utaltunk. Egy hatalmas centrifuga ez, mely a villanymotorok forgó részét, a rotort vizsgálja.
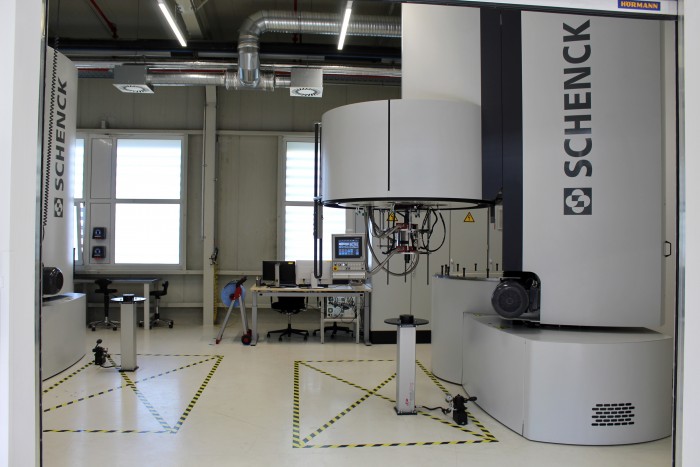
A rotortesztelő gép padlótól plafonig betölti a teret
A rotorok percenként akár 15 ezres fordulatszámon is működhetnek egy elektromos motorban – mondani sem kell, a szám jóval nagyobb, mint a belső égésű motorok fordulatszáma. Működése közben akár a 180 Celsius-fokot is elérheti a szerkezet, ami már fizikai elváltozásokat is okozhat a hőtágulás miatt.
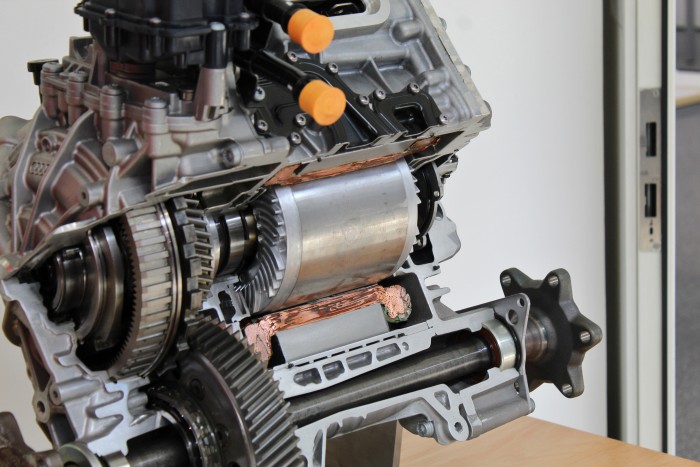
A középső fémhenger a rotor, ezt nyúzzák négy hétig
Ezt vizsgálja a centrifuga, melyben a rotort rögzítik. A hermetikusan zárt térben egy-egy rotort négy hétig folyamatosan gyorsítanak és lassítanak, mellyel 200 ezer kilométert szimulálnak. Vizsgálat közben lézerek pásztázzák az egységet, melyet időnként azért a hétköznapi használat négyszeresével is megterhelnek: a gép 63 ezres fordulaton is pörgetheti a rotort.
Ennél a terhelésnél előfordul, hogy az anyagok belső feszültsége annyira megnő, hogy szétrobban a rotor. A centrifugát erre is felkészítették, három réteg acél fogja meg a szétszálló repeszeket. A tönkretétel-vizsgálat gyorsan végbe megy, ezt egy perc alatt lezavarja a gép.
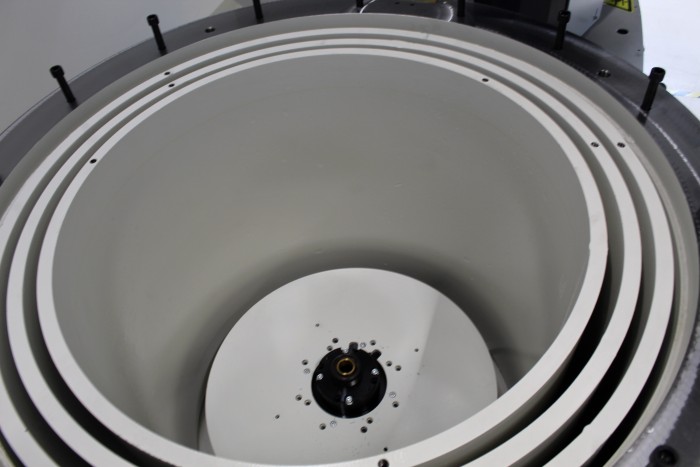
Három acélréteg véd mindent és mindenkit a szétszálló repeszektől
Nem hagyhattuk ki a nagy klasszikus, a görgős fékpad meglátogatását sem. Talán ennek a képe ugorhat be legelőször a laikusok számára, ha autók teszteléséről van szó. A szerkezet számára kialakított helyiségben nagyon hasonló körülmények teremthetőek ahhoz, mint ami a járművet az úton fogadja. A hajtásláncot tartósan lehet itt terhelni már az autóba beépített állapotában, miközben a rendszer a légellenállást, a különféle útfelületeket, valamint az emelkedőket és a lejtőket is képes szimulálni. Mivel a hőmérséklet stabil és a forgalom sem zavar senkit, az itt kapott eredmények konzisztensebbek, mintha közúton tesztelnék az autókat.
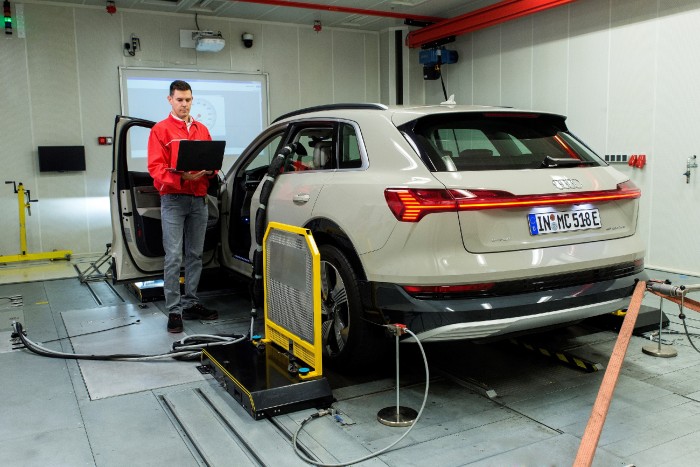
A sárga elemek tartják stabil pozícióban az autót, oldalra nem törhet ki még 280 km/órás sebességnél sem
A padon akár 280 km/órás sebességet is elérhetnek az autók. Menetszél is éri a kocsikat teszt közben, a motornak és a fékeknek ugyanis kell a hűtés: legfeljebb 130 km/órás légmozgást képes generálni a légtechnika két, egyenként 55 kW-os motorja. A padra állított Audikat ember és gép is vezetheti.
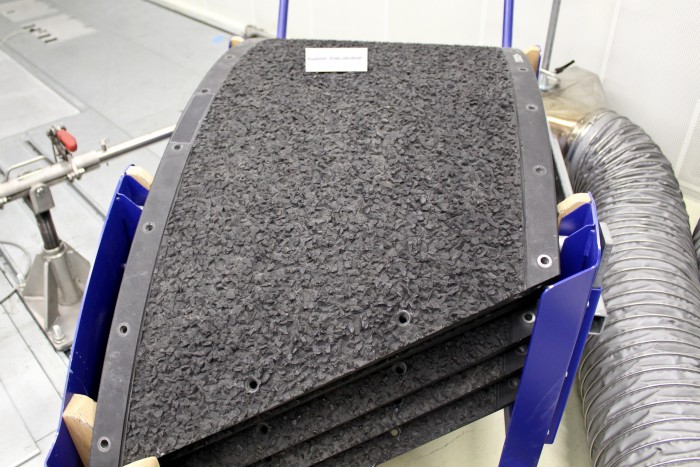
Érdes útburkolatú görgőelemek, melyeket összekapcsolva egy kétméteres hengert kapunk. Ezen száguld a tesztelni kívánt jármű
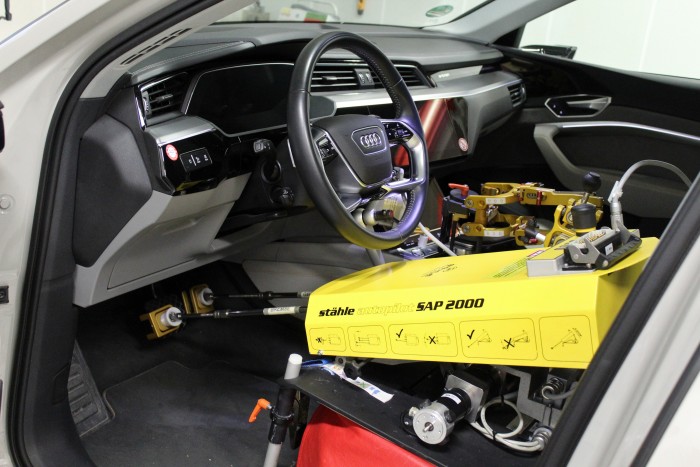
Minden a gép kontrollja alatt
Egy autó elcsendesítése nem olyan egyszerű dolog, mint gondolnánk, hiszen maga a kasztni egyfajta erősítőként viselkedik, minden zajt hangosabbá tesz. Némi hangszigetelés persze javít a helyzeten, ahogy az az alábbi videóban is látszik. Érdekesség, hogy a szigeteléssel kapcsolatos elemzések jelentős részét már a mesterséges intelligencia végzi, a valós tesztek legtöbbször már csak a számítógépes modell adatainak megerősítésére szolgálnak.
Tanulságos látogatás volt ez még úgy is, hogy a bemutatott eszközöket nem láthattuk működés közben, pedig az adhatta volna meg a túra sava-borsát. De enélkül is bepillantást nyerhettünk azonban egy olyan világba, ahol nem csak arra jók a magyar autógyári dolgozók, hogy a sor mellett gürizzenek, hanem bőséggel akad lehetőség arra, hogy szellemi képességeiket kamatoztassák.