Ipolytölgyesen nagyjából 500-an élnek. Annyira pici falu, hogy a település eleje táblától látni a település vége táblát, a telefonra meg már jön az SMS, hogy Üdv Szlovákiában! De csak az Ipoly sodorja ennyire közel a jelet, még Magyarországon járunk, az viszont feltűnhet, hogy a lakóházak mögött egy jókora szürke épület tornyosul. Ez a MONO gyárépülete, ami 1989 óta áll itt, ezen az egészen eldugott helyen, és ontja magából a legminőségibb autóipari termékeket.
Belső díszítőelemeket készítenek itt Lamborghinikhez, BMW-khez, Audikhoz, Jaguarokhoz és a legújabb Range Roverhez. Ezek az elemek kulcsszerepet játszanak abban, mennyire jó minőségérzetű az autó. Szem előtt vannak, kéz alá kerülnek, amikor a szemlélő csak először beleül a kereskedésben, ezer százalékig biztos, hogy végig simít rajtuk a kezével. Így a kockázat és a felelősség óriási. Ami Ipolytölgyesen készül, az meghatározza az említett autók minőségét, megítélését.
Több mint 30 éve készülnek belső elemek a MONO-nál
Még rengetegen élénken emlékeznek a berlini fal 1989. november 9-i leomlására, de ugyanekkor mutatkozott be a világnak a Nintendo forradalmi játéka is, a Game Boy. Ebben az évben alapította Francois Bandura is a MONO gyárat Ipolytölgyesen, és azóta az autóipar élvonalába sikerült feltornázni a vállalatot.
Itt rend van, a biztonsági őr minden autót orral egymás felé fordíttat a parkolóban, mert Francois szerint úgy van rendjén. Mivel ő nem csak egy fej, egy sokmilliomodik cégvezető, aki valahonnan távolról irányítja a vállalatát, hanem amikor csak lehet, bejár dolgozni, fontos, hogy olyan legyen a hely, amilyennek ő megálmodta.
Tanult foglalkozása szerint bútorasztalos, kézzel készült míves ajtók díszítik azt a termet, ahol fogadott bennünket, az ő saját keze munkája, így kérdés nélkül elhiszem, hogy ha valaki tudja, milyen a szép fa díszbetét, akkor az ő lesz. Bármennyire is a modern autóipar élvonalbeli modelljeihez készülnek itt az alkatrészek, a hangulat családias. Francois mindenen rajta tartja a kezét, a részlegek vezetőivel baráti a kapcsolata. Ha egy új gépsor felállítását kell koordinálni, abban is segít. Így volt ez a tavaly felépült új csarnok beüzemelésekor is, a hét minden napján, reggeltől estig felügyelt és segített, végső soron ez még mindig az ő álma, ami mára közel a legmagasabb szintre jutott el.
6 milliárd forintból külön gyárcsarnok a Range Rovernek
Korábban is volt megrendelésük a Jaguar Land Rover-csoporttól, tavaly azonban kizárólagos beszállítói megállapodást kötöttek velük. Minden új Range Rover modellhez az ipolytölgyesi MONO szállítja a belső díszítőelemeket. Ez évente 120 000 autóhoz elég belső díszítőelemszettet jelent, minden Range Roverbe 10-12 elem kerül, attól függ, hogy hány üléses kivitelről beszélünk.
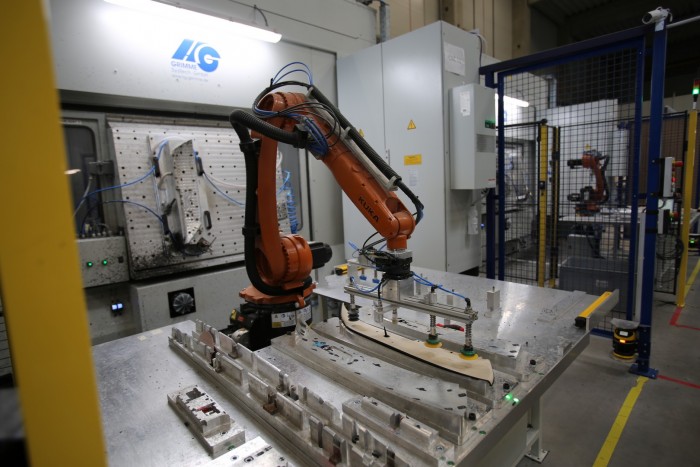
Vákuumal emeli fel a robot a munkadarabot
Bő 200 új munkahelyet jelentett ez a fejlesztés a MONO-nál, így már több mint 700-an járnak be dolgozni Esztergomról és környékéről. Aki nem autóval, az a cég saját, ingyenes buszjáratával jár. Csúcsminőségben dolgoznak a legmodernebb gépekkel, de olyan saját fejlesztésű gyártósoruk is van már, amihez hasonlót egyelőre a piac egyik hasonló szereplője sem használ, de jelentősen javít a hatékonyságon. Ezt a robotizált folyamatot meg sem mutathatjuk, de egy olyan munkafolyamatról van szó, ahol az emberi alapanyag-mozgatást robotokkal váltották le. Ez a gyártósor házon belüli fejlesztés és kivitelezés, mert a MONO nem csak egy gyár, fejlesztőközpont is.
Kérésre és saját kútfőből is dolgoznak
A megrendelő sokszor konkrét igényekkel áll elő. Fabetétet szeretnének több árnyalatban, vagy magas fényű zongoralakkot, esetleg alumíniumot szálcsiszolva vagy festve, akár festve és szálcsiszolva, vagy karbonszálas műanyagot, vagy olyan fabetétet, amin átüt az alumínium, csíkokban, vagy konkrét mintával.
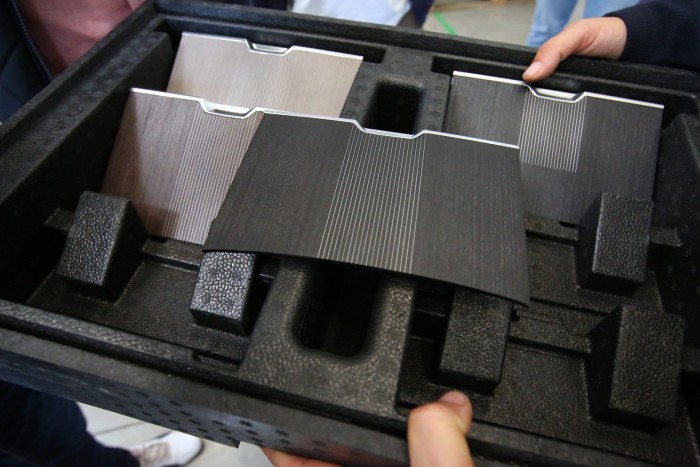
Az alumínium alapot bemarják, majd rápréselik a fát, így ütnek át az alumínium vonalak
Ez azonban fordítva is működik. A MONO-nál folyamatosan dolgoznak új megoldásokon, érdekes belső elemeken, különleges anyagokon. Így lehet az, hogy a bemutatófalon olyan, Jaguarhoz tartozó belső elemeket is látunk, melyekbe fekete kagyló héjának a durva törmelékét öntötték, némelyik még át is látszik, így hátulról megvilágítható. Ez még csak prototípus, a mellette lévő ragyogóan fehér, kerámiaport tartalmazó festékkel bevont fedelek viszont nem. Ilyen belső elemet más márkák autójában nem láthatunk, a Jaguar Land Rover saját fejlesztése, és csak itt készül, csak a Range Roverhez.
Fa a Range Roverhez, alumínium az Audihoz és Lamborghinihez
Egy milliméternél vékonyabb falemezből készülnek a Range Rover belső elemei. Az alapanyag a világ minden tájáról érkezik, hogy honnan, az attól függ, hol jó a minőség, és milyennek kell lennie a végeredménynek. Lakkozott és nyílt pórusú betétek is készülnek. A falemezt először formára vágják, a kivágott kartonlapszerű alkatrészt pedig ezután fröccsöntik, így kerül rá a műanyag rész.
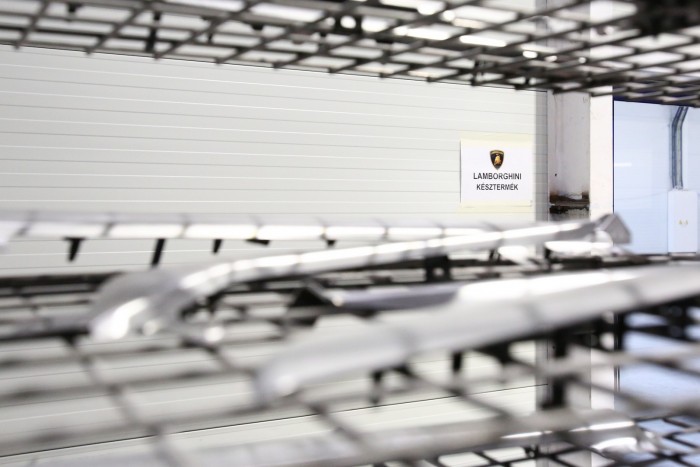
Lamborghini Urushoz készülnek a belső elemek
Kézműves munkára is szükség van, a falemez bonyolult hajlításainak csiszolását nem bízzák robotokra, túl vékony ahhoz az anyag. Emberi kezek pontos munkájára van szükség, érintésre érezni csak, hol kell még csiszolni, és hol vékonyodhatna el tőle az anyag túlságosan. Ezután festik és lakkozzák az elemeket, majd mehet csomagolásra és szállításra.
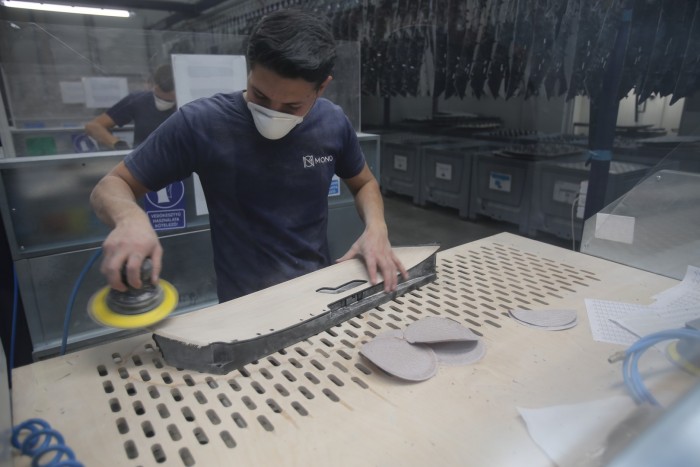
A fa réteg finomcsiszolását kézi munkával végzik, nem bízzák robotokra
Más az eljárás az alumíniummal. A Lamborhini Urushoz készülő belső elemeket először formára vágják, előhajlítják, majd formára préselik, ezután kerülhetnek rá a fröccsöntött alapra. Az Urushoz készülő elemeket többszörösen szálcsiszolják, több irányból, majd anodizálják, vagy más néven eloxálják, hogy ne korrodálódjon. Az alumínium ezeken az elemeken vastag, egy milliméter körüli, így egyrészt nehéz, másrészt hideg, ez pedig fontos, ha fémnek látszó tárgyat tapintunk, az élményhez mindenképp hozzáad.
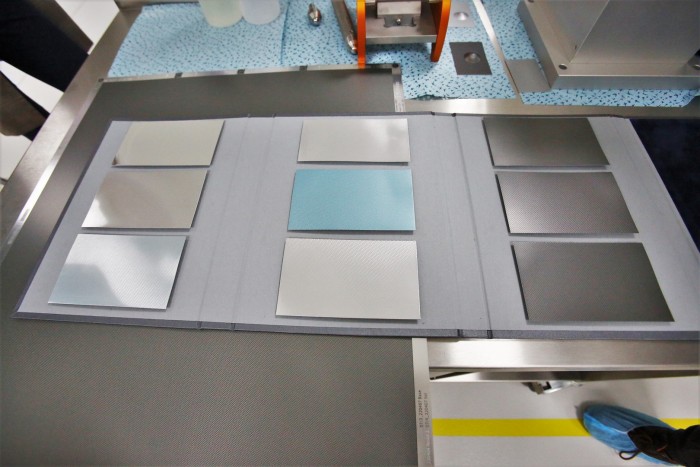
Kilenc lépésen megy keresztül, mire elnyeri a végleges felületet
Megint csak másik technológiával készülnek az Audi Q3 belső elemei. Pontosabban az az egyetlen darab, ami a műszerfalat díszíti. Szintén több irányból szálcsiszolt alumínium, de csak bonyolultnak tűnő mintákban látszik rajta a csiszolás. Ehhez a lemezeket maszkolni kell, speciális nyomtató viszi fel a csiszolást tűrő festékanyagot, amit csiszolás után eltávolítanak, majd mehet rá egy másik maszkolóminta, és újabb csiszolás, majd festés.
A folyamat hosszú és hajszálvékony a tűréshatár, ehhez tisztaszoba kell és védőöltözet. A végeredményt centikről kell vizsgálnunk ahhoz, hogy lássuk a felület részleteit, messziről fel sem tűnik, mennyi munkába kerül, de még egy Q3-nál is rászánja ezt az Audi.
A legtöbb folyamat automatizált, de kellenek az emberek
Nem csak a fa elemek csiszolásához kell az emberi munkaerő. A festékeket kézzel cserélik a festőrobotoknál, az Audi elemeinek nyomtatóinál is emberi munkaerőre van szükség az elemek pontos behelyezéséhez, és persze a minőségellenőrzésen is emberi szemek szúrják ki a hibákat. A Range Rover során, napi 400 darabos gyártás mellett, 30-35 elem esik ki hiba miatt naponta.
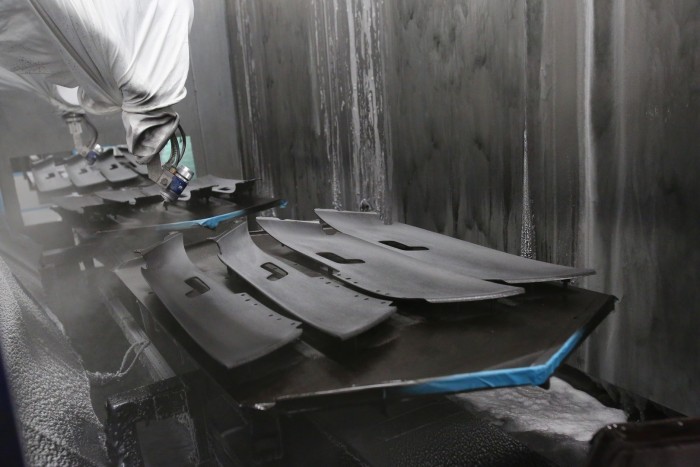
Robotok festik, a szálló festékport pedig vízfüggöny köti meg
Emberi munka határozza meg a kutatás-fejlesztést is, folyamatosan dolgoznak a gyártósorok jobbá tételén, ahogy az új elemek kivitelezésén és a prototípusok készítésén is. Ha érkezne egyedi megrendelés a Range Roverhez, azt is a MONO gyártaná le az ügyfélnek, ennyire kötött a szerződésük a Jaguar Land Roverrel.
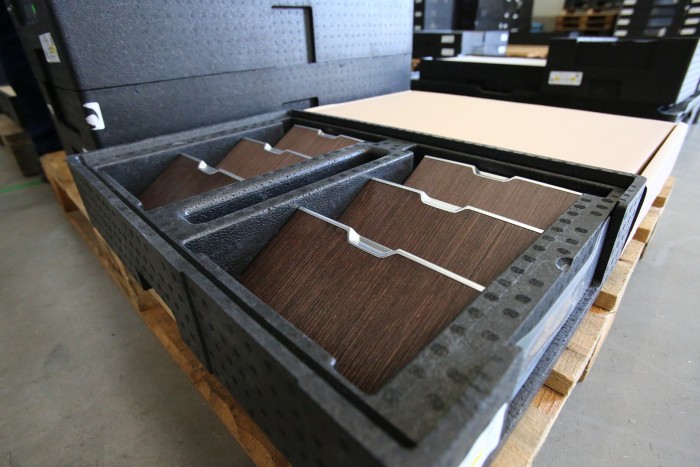
Alumínium alapra készülnek a fedelek, karbonszálas, fa, alumínium és még kerámia bevonatú is lehet
Az olyan prémiummodellek, mint a Range Rover, a Lamborghini Urus vagy a Mercedes A és B osztály mellett az Aston Martin DBX belső díszítőelemeinek egy része is itt készül.
A luxusmodellek vásárlóközönsége elvárja a belső minőséget és hajlandó áldozni is rá. Ezekben a modellekben a MONO felel ezért az élményért, és ezen a szinten csak a tökéletes elfogadható, ami itt, Magyarországon, egy kis faluban készül.