Folytatjuk a Continental két napba sűrített, ezernyi témát és területet érintő gyorstalpalójának feldolgozását. Már túl vagyunk a különféle állapotú abroncsokkal végzett saját fékteszten, meglátogattuk az előző napi vihar miatt éppen használaton kívüli, amúgy az ellenőrzött körülmények között végzett fékteszteket végző állomást, láttunk jégpályát, és megnéztük, hogyan mérik a különféle mintájú abroncsok által keltett zajt. De maradt még érdekesség bőven, kiderítjük mennyivel lehet gyorsabban végigmenni egy vizes pályán átlagos, illetve prémiumkategóriás, sportos használatra tervezett gumival, és megnézünk azt is, hol és hogyan készülnek a futófelület minták prototípusai, és a tanulmányautók meghökkentő mintái, majd kiderül, hogyan lesz a leharcolt teherautóabroncsokból ismét új gumi.
Maradjunk még egy kicsit az előző részben jobban megismert Contidrom-ban és azon belül a folyamatosan locsolt, vizes tesztpályán, ahol a noname és a prémium – Continental – sportgumi közötti teljesítménykülönbséget is saját bőrünkön érzékelhettük. A két részre osztott csapat szerencsésebb feléhez tartoztunk, mi az átlagos gumival vághattunk neki az aszfaltkarikának, és utána váltottunk a várakozások szerint jobban teljesítő Continental-ra. Normál körülmények között autózva nem tűnik fel a különbség a kétféle abroncs között, így egészen az első komolyabb gázadásig kellett várni, amíg egyértelművé vált a márkás gumi előnye.
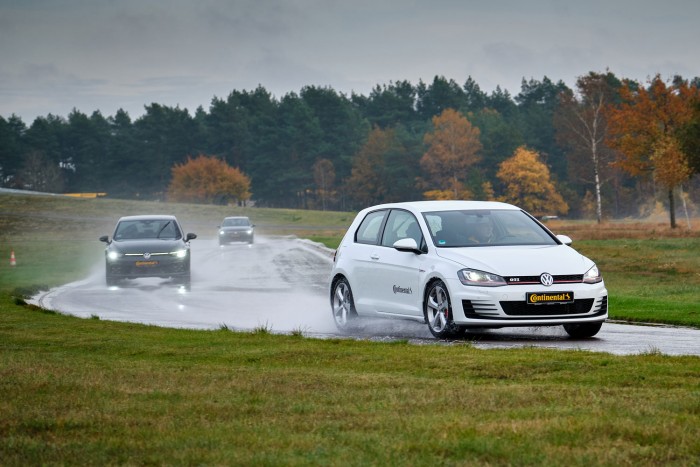
Érezhető és mérhető is a különbség a prémium és az átlagos abroncs teljesítménye között
Ugyan kikapcsolt, illetve sport módban nagyon megengedő ESP-vel mindkettővel elkapart a Golf GTI, de érezhetően később a drágább abronccsal, és a kanyarokban is annyival stabilabb volt a Continental gumikon az autó, hogy azt bárki könnyen észrevehette volna. Csak csendben írom le, hogy sokkal szórakoztatóbb volt keresztbe csúszkálni a vizes pályán a csöves gumival, mint stabilan kanyarodni, de ez maradjon köztünk. Ha időre ment volna, vagy nem pályán randalíroztunk volna, ahol senkiben és semmiben nem tudtunk kárt tenni, akkor persze egyértelműbb lett volna a választás. Mindenesetre a GPS-szel mért körök átlag- és csúcssebessége – utóbbi 92 és 105 km/óra – közti különbség sokat elárul.
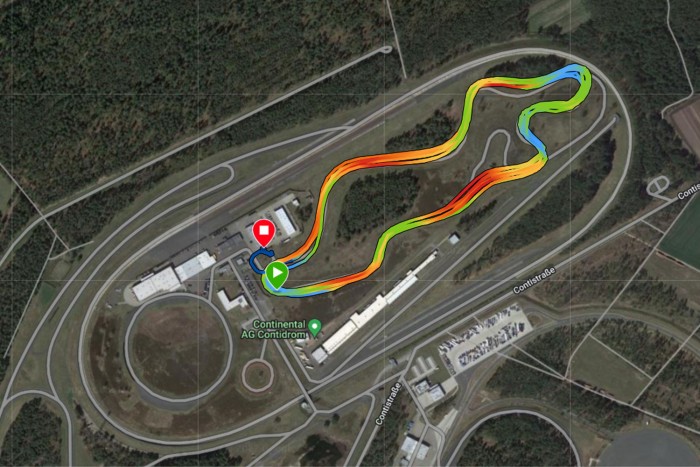
Így fest a locsolt pálya, a piros szakasz a leggyorsabb rész
Mintafaragók
Újabb labirintusban tekergés következik, a régi épület pincéjétől a padlásig mindenhol jártunk, mire megérkeztünk abba a laborba, ahol többek között az újonnan megálmodott abroncsmintákat vágják. Vagy kézzel, vagy robottal. Hogy ennek mi értelme van? Nyilván a spórolás, hiszen egy eddig nem létezett új abroncs legyártása ötszámjegyű összeg is lehet, – természetesen euróban – így sokkal gyorsabb és rentábilisabb elsőre néhány tesztdarabot elkészíteni belőle, akár kézi munkával is.
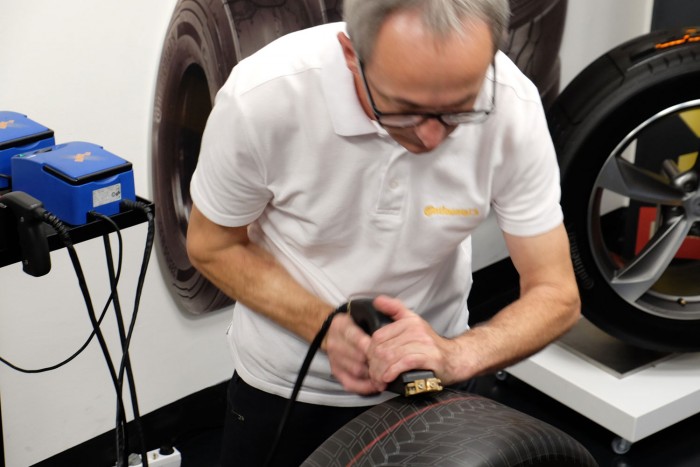
Szinte már művészek, akik itt dolgoznak
Itt pont azt csinálják. A fóliára nyomtatott mintát először átrajzolják a gumi felületére, majd saját tervezésű kézi szerszámmal „kifaragják” a mintát. Különböző alakú, fűtött, éles szerszámfejjel vágják a vízelvezető barázdát és a rafináltabb lamellákat is. Kipróbáltuk, erő és tapasztalat is kell az eszköz rendeltetésszerű használatához, de bele lehet rázódni. A másik lehetőség, hogy precízebb és fáradhatatlan robotokra bízzák a munkát, amik bármikor milliméter pontosan képesek megismételni a mintavágást.
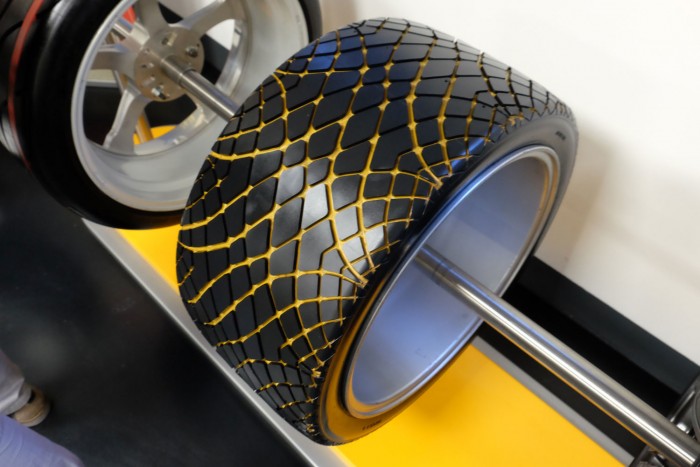
Extrém megjelenésű, kétszínű abroncs
Van más feladata is ennek a részlegnek, a különleges, egyedi abroncsokat is itt gyártják. Például tanulmányautókra, kiállításokra, extra autókra. Ezeknek nem kell jól tapadniuk, nem számít, mennyi vizet vezetnek el, vagy hogy mennyire zajosak, kopásállók, lényeg, hogy jobban nézzen ki tőlük az autó, amire felszerelik.
Újrafutózás
Egy másik üzemrészen a teherautóabroncsok újjászületését vesszük végig. A rommá kopott és legfeljebb 8 éves, kizárólag Continental márkájú abroncsok hatalmas halmokban várják, hogy egyszer majd új gumiként hagyják el a gyárat. Alapos, külső belső átvizsgálással kezdődik a folyamat, ahol a menthetetlen abroncsokat gyorsan kiszórják a sorból. Míg a képzett szakemberek a látható hibákat keresik, addig egy gép átvilágítja az abroncsot, miközben a gumi mélyében rejtőző hibákat keresi. Érdekes, hogy a méretes lyuk, a durva kopás nem jelenti azt, hogy az abroncs menthetetlen, ezeket gyorsan, hatékonyan javítják a későbbiekben.
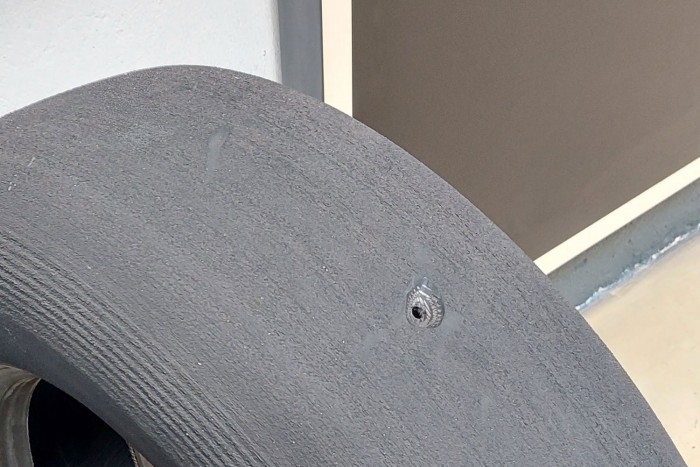
Ez a lyuk még probléma
Maga a folyamat nagyon sok kézi munkát, emberi szakértelmet kíván, de végső soron a gyárnak, a vevőnek és a környezetnek is jó. A gyár a beletett rengeteg emberi munka ellenére is hamarabb végez egy felújítással, mint egy teljesen új abroncs elkészítésével – az abroncs nagy részét adó alap már készen van – a vevő kedvezőbb áron jut az újjávarázsolt abroncsért, a környezet meg örülhet, hogy hulladék helyett új abroncs készült a látszólag reménytelenre kopottból.
Ha eddig megfelelt, akkor átlagosan 8 kilogramm gumit darálnak le az alapról, – ennek egy részét később újra felhasználják – majd a pucér vázra a friss futófelület mellett új oldalfalat is építenek, végül az abroncs megy a kemencébe, ahol 150 fokon egy órán át készre sütik. Az elkészült abroncsok minden tekintetben olyanok, mint az új, így akár ismét 130 ezer kilométeren át használhatók. Sajnos másodszor már nem újítják fel őket, pedig állítólag építkezéseken, bányákban, ahol nincs nagy sebesség, még simán lehetne azután is használni őket.
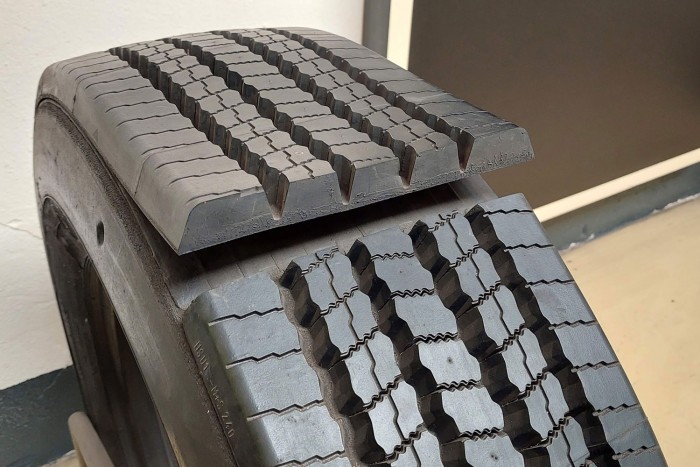
Új futó és oldalfelületet kap a teherabroncs a felújítás során
A teljes folyamat végén jön a nyomáspróba, amikor az elkészült abroncsot egy zárt szekrényben az automata 8 barra fújja, és megvizsgálja. A problémás gumik itt hatalmas robbanás mellett azonnal elvéreznek, amire általában a csarnok dolgozói és a közeli irodában szorgoskodók is összeszaladnak. Szerencsére nem gyakori ez a zajos műsorszám, az elmúlt öt évben négy ilyen eset történt csupán.
Bár kinézetre a felújított gumi pont úgy néz ki, mint egy vadi új, a gyár segít megkülönböztetni a kettőt egymástól, így az újraépített gumi oldalfalára felírják, azt is, hogy „RE”. Úgy a tuti.
.