Gondolnád, hogy a gumiabroncsgyártás lehet környezetkímélő és megúszható a teljes folyamat CO2-kibocsátás nélkül is? Pedig egy óriási, több százezer négyzetméteren elterülő, évi 18 millió darabos kapacitással üzemelő gumigyár is működhet fenntartható módon. Elmondjuk, hogyan, mert nemrég épp egy ilyet látogattunk meg Portugáliában.
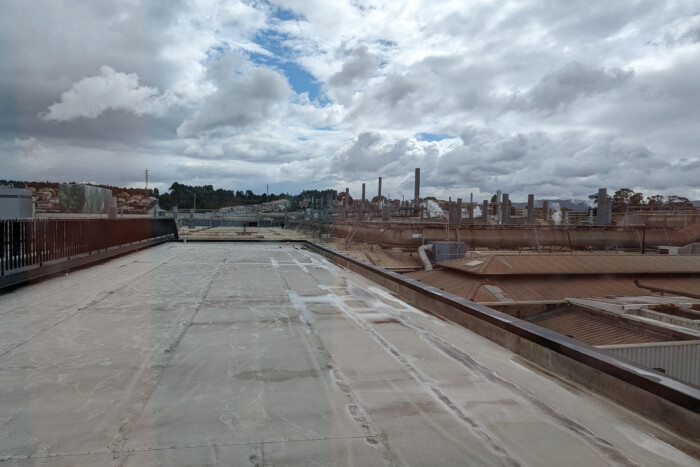
A gyár közel van a lakóházakhoz, így nemcsak zöldnek, hanem csendesnek is kell lennie
Lousado
A Portótól szűk 30 kilométerre fekvő gumigyár magja nem új, a Mabor névre hallgató helyi gumigyártó vállalkozást 1938-ban alapították, bár az abroncsgyártás csak a második világháború után, 1946-ban indult be az akkor természetesen még sokkal kisebb üzemben. Hamar sikeres lett a vállalkozás – amihez az is hozzájárult, hogy monopolhelyzetben volt a cég –, a termelés 1950-re már elérte az évi egymillió darabot.
1970-ben új irányba nyitott a cég, az észak-európai országokba kezdett téli gumikat – Winter-Jet néven – exportálni. Az igazi változás 1990-ben következett be a gyár életében, amikor a Continentalhoz csatlakozott a cég. Ekkor komoly fejlesztések kezdődtek a gyárban, ami bővült, hatékonyabb és zöldebb is lett az évtizedek alatt és már 1994-ben napi 20 ezer abroncsra nőtt a kapacitása.
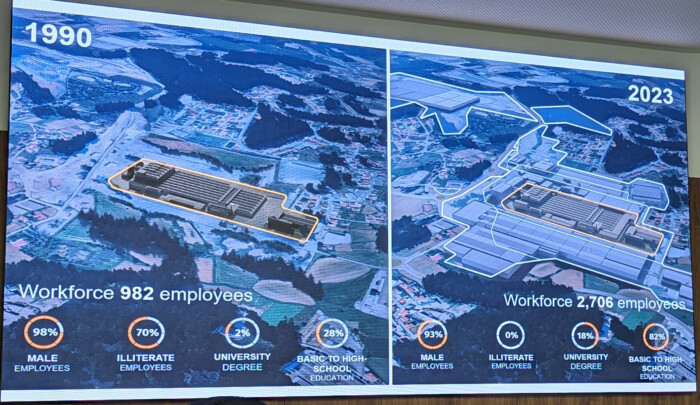
Ekkorát változott méretben és munkaerőben a portugál gumigyár 1990 és 2023 között
1990-ben még csupán 982 dolgozóval kezdték a Continental zászlaja alatti termelést, ez 2023-ra 2706 főre nőtt, kezdetben a munkások 98 százaléka volt férfi, ez tavaly már 93 százalék volt – úgy látszik, a gumigyártás még nem az a terület, ami népszerű a női munkavállalók körében – és nagyot nőtt, 2-ről 18 százalékra az egyetemi, főiskolai végzettséggel rendelkezők aránya is. Persze eközben nőtt az üzem területe is, az 1990-es 40 ezer m²-ről 315 ezer m²-re.
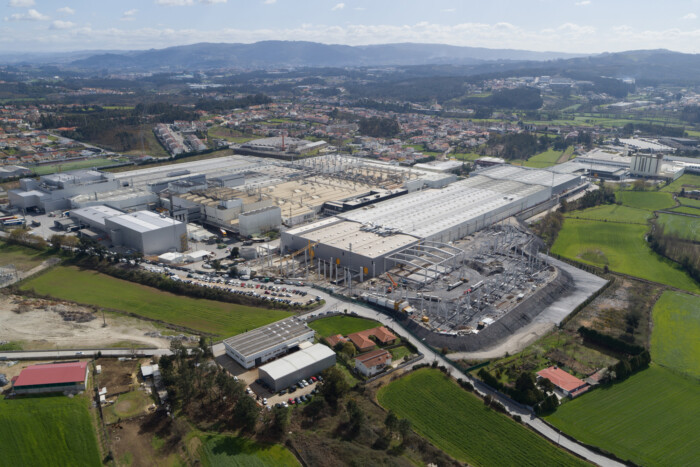
Most így néz ki a gyár a magasból
Jelenleg személyautókra és munkagépekre való, traktorgumitól a bányákban használt, óriási dömperekre való abroncsig mindenfélét gyártanak a lousadói üzemben, a gyár kapacitása pedig az évi 18 millió darabot is meghaladja.
De mitől zöld?
A Continentalnál mernek nagyot álmodni, a cég tervei között szerepel, hogy legkésőbb 2040-re az összes abroncsgyárukat – ez 16 országban 20 üzemet jelent – CO2-semlegesre állítják át.
A lousadói üzem már elérte ezt a célt, ahol a gyártási folyamat leginkább energiaigényes részét, a vulkanizáláshoz szükséges gőz termelését a korábbi gázról elektromos üzeműre állították át. Persze az sem mindegy, hogy az elektromos áramot hogyan állítják elő, ezt részben saját, az üzem épületeinek tetején található napelemek termelik meg, részben pedig vásárolják.
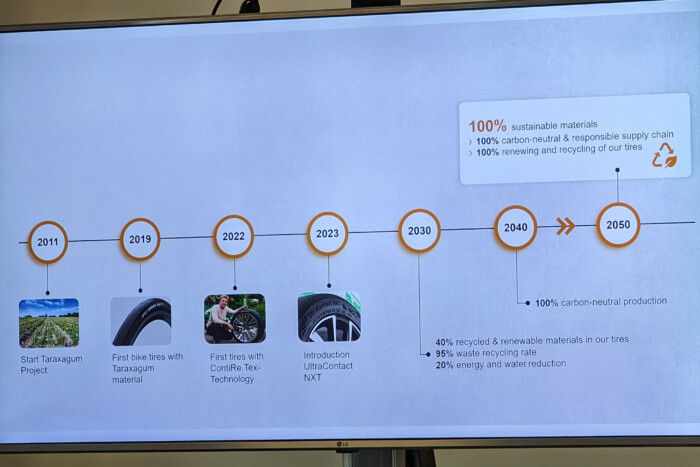
Nem ma kezdte a Continental a termelés zöldítését. Az ábrán a korábbi fontos pillanatok és a jövőbeni célok láthatók
Könnyű dolga van a portugál üzemnek, Lousadóban a Nap átlagosan hét órát süt naponta és télen is kijön a napi négy óra. A vásárolt elektromos energia pedig kizárólag megújuló forrásból származik. Ha szükség lenne rájuk, a termelés biztonsága érdekében továbbra is rendelkezésre állnak a gázüzemű kazánok is. Emellett a Continental az iparági átlaghoz viszonyítva a legkisebb energiafelhasználással állítja elő az abroncsait, csak 2023-ban a cég gumiabroncsrészlege 160 energiatakarékos projektnek köszönhetően összesen mintegy 150 gigawattórával csökkentette az éves energiaszükségletét.
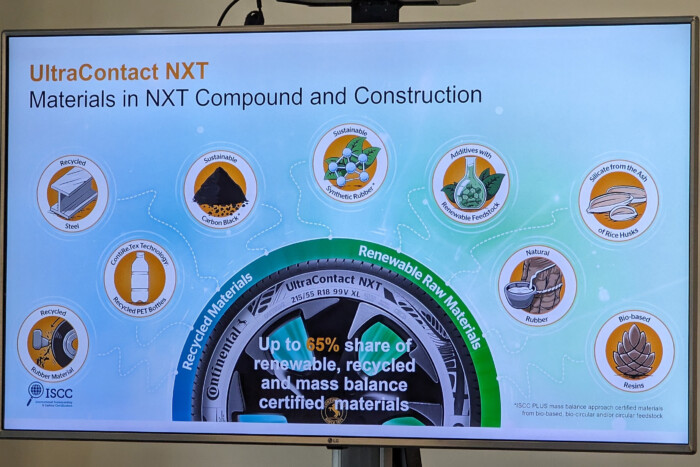
Reciklált és fenntartható komponensek az UltraContact NXT-ben
Az iparági átlagnál kisebb a vízfelhasználás is, itt 50 százalékkal kevesebb fogy belőle, mint máshol. De nemcsak a gyártási folyamat, hanem a végtermék is zöld. Az új UltraContact NXT 65 százalékban tartalmaz újrafelhasznált vagy megújuló alapanyagokat. Ilyen például a reciklált acél, a PET-palack, vagy éppen a rizshamu, és a növényi eredetű gyanta is.
Persze nincs megállás, a távlati tervek között szerepel, hogy 2030-ra 40 százalék fölé viszik a fenntartható és újrafelhasznált anyagok arányát a gyártásban, legkésőbb 2050-re pedig 100 százalékra emelik.
UltraContact NXT
Az új UltraContact NXT mérettől függően már most 65 százalékban tartalmazhat ilyen anyagokat, miközben a gyártó ígérete szerint nem kell kompromisszumot kötni a teljesítmény terén sem: az abroncs gördülési ellenállása, a vizes felületen nyújtott tapadása és a gördülési zaja egyaránt kiváló, A minősítést kapott. Az új UltraContact NXT abroncs, ami az elektromos autók igényeinek is megfelel, egy darabig párhuzamosan fut majd a korábbi UltraContacttal, bár lesznek olyan méretek, amik csak az új és olyanok, amik csak a korábbiban érhetők el.
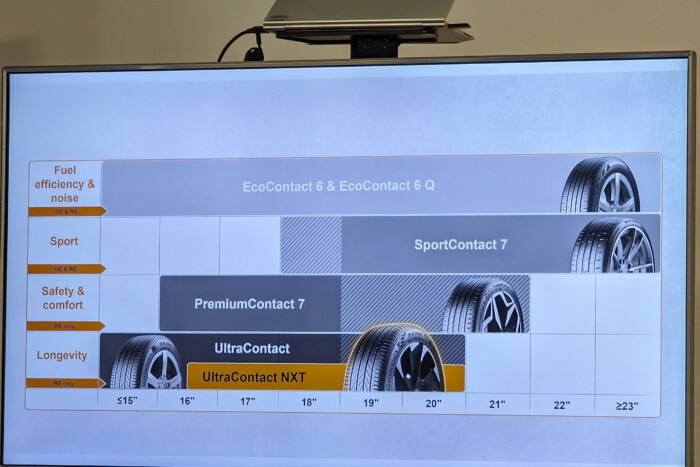
A régi és az NXT változat méretei nagyjából lefedik egymást, de idővel az NXT-ből is lesz mindenféle méret
Az alapvető folyamatok ugyanazok, bár a technológia és felhasznált anyagok nagyot változtak 1950 óta:
Így készül
Alapvetően kétféle gyárlátogatás létezik. Az egyik, ahol fényképezőgéppel a kézben ballaghatunk végig az üzemen, és azt fotózunk, amit csak akarunk, a másik pedig, ahol még a telefont is elveszik, mielőtt belépünk a csarnokokba. A Continental a gumigyára bemutatásakor az utóbbit választotta. Hogy milyen logika szerint döntik el, hogy a szervezők hagynak-e saját képeket készíteni vagy sem, azt a hosszú évek alatt eddig nem sikerült megfejteni. Bicikli-összeszerelő üzemtől az autógyáron át a gumigyárig mindkét változatra volt már példa. Úgyhogy most nincsenek saját képek.
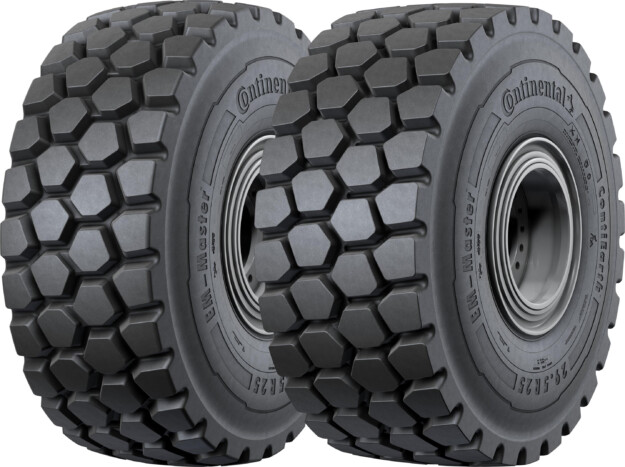
Egy kb. 600 kilogrammos abroncs elég impozáns tárgy
Mi ezúttal a személyautókra szánt abroncsoknál kezdünk, méghozzá egész az elején, a halmokba rakott nyersgumitornyok között. Az abroncsgyártás folyamata kevéssé szórakoztató leírva, így nem is húznám sokáig. A lényeg az, hogy szinte minden folyamatnál van minőség-ellenőrzés, és az elkészült abroncsokat egyesével ellenőrzik még egyszer a folyamat legvégén.
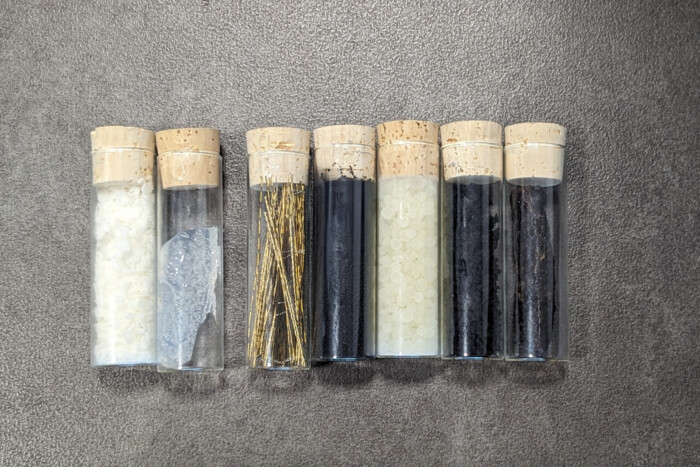
A zöldkomponensek, amik az abroncsba kerülnek
A szépséghibás abroncsok mennek még egy kört, kurtábbra vágják rajtuk a gumiszőröket, vagy megtisztítják az oldalfalat, de amelyiken komoly hibát vesznek észre, az megy a selejtek közé. Előtte azért biztos, ami biztos, óriási lyukat vágnak az abroncs oldalába, hogy véletlenül se lehessen azokat felhasználni.
Akit az abroncsgyártás minden egyes mozzanata érdekel, és nem kap kiütést attól, hogy 17 percen keresztül James Bond jellegű zenét hallgasson, az ezt a gyári videót nézze végig:
Innen a jóval látványosabb, szellősebb, munkagépekre szánt abroncsok gyártósorához indulunk. Maga a folyamat itt is ugyanaz, csak a gépek és a készülő abroncsok váltak óriásivá. Illetve az abroncsok kemencében töltött ideje is többszöröse – a hőmérséklet és nyomás megegyezik – annak, mint amit korábban láttunk.
Modernebb a logisztika is, itt önjáró robotok cipelik a néha akár 600 kilogrammos, speciális igényekre tervezett és gyártott hatalmas gumikat. Van itt minden, óriási, terepmintás traktorgumi, bányagépekre szánt, több száz kilós abroncs, akkora bütykökkel, mint egy dinnye, és bitang teherbírású, rakodógépgumi is. Talán ez az üzem leglátványosabb része az elkészült abroncsokat halszálkába – így éri a legkisebb terhelés a gumikat szállítás közben – pakoló robotmunkás mellett.
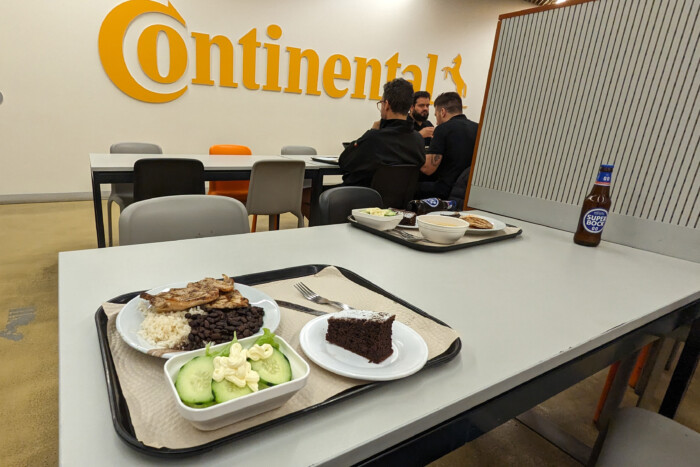
Üzemi étkezde, babbal, rizzsel, alkoholmentes sörrel
Hogy teljes legyen az üzemlátogatás-élmény, a jellegzetes gumiszagtól a futószalagok között menetelésen át a robotokon csodálkozásig még egy ebéd is belefért az üzemi konyhán. Ami meglepően nagy választékkal dolgozik, grill, hal és vega menük közül választhattak aznap a dolgozók. Van alkoholmentes sör is, de az étellel ellentétben az igazán csapnivaló, nem is itta senki rajtunk kívül. Viszont az itt készült gumik minőségén ez nem változtat.